Plane Wave Imaging of Coarse Grain Material
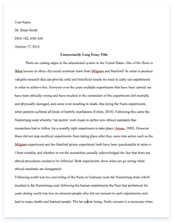
- Pages: 3
- Word count: 544
- Category: Nuclear Energy
A limited time offer! Get a custom sample essay written according to your requirements urgent 3h delivery guaranteed
Order NowThis research project aims to produce some helpful findings in improving the defect detectability of Ultrasonic Non-Destructive Testing (NDT) on coarse grained materials especially using Plane Wave Imaging method (PWI). Common coarse-grained materials such as Copper and Cast stainless steel are widely used in industry. An example is the container of nuclear waste disposal which is a large copper vessel. This cylinder will probably have diameter about 1 meter and length over 5 meter with wall thickness approximately 50 millimetre. In order to detect surface breaking, subsurface cracks, holes, and manufacturing defects under services condition, ultrasonic examination and radiography are applicable (Bowyer and Crocker, 1996).
However, metallic specimens absorb considerable amount of energy in the X-ray which makes this method slow and expensive compared with Ultrasonic testing. Also, the radiography can cause serious health issue to human body (Esabna.com, 2020). Besides this specific case, PWI is studied in particular because of the considerable depth of penetration, the efficiency of imaging processing and the image quality. Another prevalent imaging method is Synthetic
Transmit Aperture, also called Total Focusing Method (TFM). The poor energy transmission in TFM limit the depth of penetration and the quality of images. These problems can be partially resolved using PWI (Montaldo et al., 2009). More detailed comparison between those methods will be given later according to the results.
Ultrasonic Non-destructive Testing
Ultrasound is a widely applied imaging technique based on high frequency sound waves. It is relatively inexpensive, flexible and not associated with carcinogenesis compared with other imaging techniques, such as Magnetic resonance imaging (MRI) and Computed Tomography (CT). More importantly, ultra sound imagine inapplicable metallic components, asopposedto CTor MRI(Morgan,2020). Production of ultra sound images is based on the wave reflection off the material. The travel time and signal strength provide information to form a corresponding image (for Devices and Health, 2020). Non-destructive Testing (NDT) has no impairment on the properties and performance of the examined materials. The discovery of piezoelectric effect by brothers Pierre and Jacuqes Cuire in 1880 made it possible of application of ultrasound to NDT. Then the pulse-echo flaw detector was developed after World War II. Ultrasonic NDT is currently one of the most commonly used flaw detecting methods. Other types of NDT include radiology (e.g. X-rays), electrical and magnetic methods (e.g. MRI), and liquid penetrant testing.
Advantages of ultrasonic NDT includes:
- Its accuracy in detecting the location of internal flaws.
- The detectable defect size can be very small.
- The high degree of penetration in most material, especially in metals.
- Testing can be done from a single surface.
- Its compatibility with devices such as microprocessor and advanced computer (Blitz and Simpson, 1995).
The limitations of Ultrasonic NDT include:
- Specimens with rough surface, irregular shape, or exceptionally small size (volume) are difficult to be inspected.
- Access to the surface of specimen is required to transmit ultrasound.
- Coupling medium (such as water and gel) is needed to help the transmission of sound energy into specimens.
- The coarse grains present in materials (such as Cast iron) will attenuate the sound transmission and cause high signal noise.
- Some linear defects, which are parallel to the sound waves, may be not detected (Ndeed.org, 2020a).
This project is focusing on the Ultrasonic NDT of coarse-grained materials. By studying the data processing of PWI, some conventional limitations might be partially resolved.