Lorex Pharmasuticals
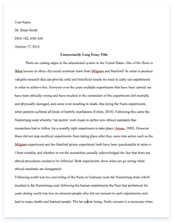
- Pages: 4
- Word count: 862
- Category: Machine
A limited time offer! Get a custom sample essay written according to your requirements urgent 3h delivery guaranteed
Order NowAbstract
This report will seek to outline and discuss the challenges faced by Lorex Pharmaceuticals. This report will detail the circumstances that dictated the challenge faced Lorex Pharmaceuticals, as well as the key areas they must consider when attempting to resolve this challenge. The report will examine the possible outcomes, and make a final recommendation based on the information provided. When developing a brand new product to be sold in the marketplace, it is crucial that all aspects of production are considered before beginning. Many factors need to be considered, including but not limited to which machinery will be used in production, where will the pricing be set, and how should the machinery be calibrated. If a company will take their time to make sure they are being as smart as possible about how they are going to proceed, it will minimize the potential for losses along the way. Executive Summary
Decision Problem
Decision Alternatives and Evaluation
Normal Distribution and Normal Tables for Determining Probabilities (Z-Approach). Checking a Data Set for Normality. Trial and Error for Maximizing Expected Value. Conditions Associated with Critical Fractile Analysis which Make it Inappropriate (News Vendor Problem Example).
Lorex Pharmaceuticals recently received approval to begin producing and selling a new drug called Linatol. They had determined how many bottles of the product would be in each case shipped, and had even determined the amount they would charge for each case. What remained to be determined was the target amount to use on the filling machines to fill each bottle. Because the bottles were to be 10 ounces each, they would not be able to sell at full price any bottles that contained less than the 10 ounce volume. They would be forced to sell any under-filled bottles at a discount on the secondary market to places like hospitals, typically at a rate of 80%.
The bottling line that was selected for use was one that could produce an average of 500 cases per 8 hour shift, which was slower than other bottling machines in use. Due to the relatively low production volume of Linatol this machine was selected since it was not currently in use and would allow other faster lines to be used for higher volume products. The machine would monitor every bottle that was filled and any that did not contain the required 10 ounces were sent to a group of special attendants that prepared those bottles for shipping to their secondary markets.
Once they selected the equipment to be used for filling the bottles, they began testing to make sure it would perform to their expectations. They would not be able to begin filling bottles of Linatol until they perfected the filling process. The first step was to fill bottles with a test liquid that was of a similar consistency as Linatol so that they would be able to mirror the results as best as possible. A target fill volume of 10.2 ounces was selected, and several tests were run. After the testing was completed, the machine had filled a total of 144 bottles, of which 12 were not filled to the 10 ounce requirement, a success rate of 91.67%. The company felt comfortable using 10.2 ounces as the fill target since the end result was within the boundaries of acceptable performance. Conclusions and Recommendations
Lorex was faced with a difficult decision. Since this was their first test with this machine filling these bottles, they were unsure of the appropriate level to program the machines with. They found that when using the fill volume of 10.2 ounces, it resulted in a standard deviation of 0.16. The rule of thumb was to select a fill level equal to one standard deviation above the desired volume. There was some concern that based on prior experience, using the one standard deviation target has resulted in bottlenecks with an excess number of underfilled bottles.
Ultimately I would suggest that Lorex maintain the 10.2 target fill volume. It exceeds the one standard deviation baseline, and provides for a small cushion for those bottles that would have been underfilled if they selected 10.16 ounces as the target fill volume. Based off of their success rate using this fill volume, they are likely to not be overwhelmed by an excessive number of rejected bottles.
Lorex took a very good approach in determining their bottling procedures for their new product. By selecting a machine that would be able to handle the demands of the production while allowing faster machines to be reserved for higher volume products they are likely to maintain an efficient production process. They also were wise in testing the machines with a liquid that has similar properties to the product. Finally, setting a fill limit slightly higher than the minimum practice will allow them to ensure that they do not become overrun with under filled bottles, while at the same time not setting the level too high which would result in an unnecessary overfill of the product.
WORKS CITED
Bodily, S. E., Carraway, R. L., Frey, Jr., S. C., & Pfeifer, P. E. (1998). Quantitative business analysis: text and cases. Boston: The McGraw-Hill Companies, Inc.