Lean Health Care Case Study
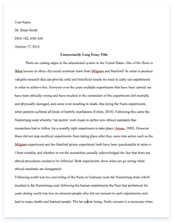
- Pages: 11
- Word count: 2514
- Category: Health Health Care
A limited time offer! Get a custom sample essay written according to your requirements urgent 3h delivery guaranteed
Order NowThis case study focuses on improving the turnaround time (TAT) and first case starts (FCS) in an operating room of Montgomery Regional Hospital. TAT is defined as the time between when a surgeon closes a cut of one patient and when he or she makes the first incision on another patient. FCS measures the time of any first cases during the day. More specifically, a delay in FCS occurs when a patient enters the surgical room later than the scheduled start time. Montgomery Regional Hospital’s objective is to decrease TAT by about 35% and to increase FCS by about 50% from its current performance (Glover, et al). The improvement activities occurred from august 2008 to December 2008.
Key Actors
Montgomery Regional Hospital, or MRH, is an investment-based healthcare institution that employs 60 full-time staff members in the Operating Room Department (MRH-OR) and handles over 6,500 surgical and endoscopy cases per year (Glover, et al). Its facility includes six Operating Rooms and two Endoscopy Rooms (Glover, et al). In its aim to improve TAT and FCS statistics, MRH formed a process improvement team specifically designed for this purpose.
The team consists of staff members from different departments of the hospital. These departments include Operation Room, Endoscopy, Central Sterile Staff and Administration (Glover, et al). Surgeons are also involved in the process through attending team meetings and providing inputs for the team.
General Nature of Problem
According to the article, factors responsible for high turnover time include:
* Recovering Patient 1
* Cleaning the OR from the procedure
* Obtaining equipment, instruments and supplies needed
* Waiting for the surgeon to begin preparing
* Preparing Patient
Due to the cost of OR time ($10–30 per minute), MRH targets TAT and FCS as their main sources for improvements. Montgomery Regional Hospital wants to reduce cost as well as improve capacity.
External Influences
The process improvement teams uses a SIPOC diagram to determine any suppliers, inputs, processes, outputs, and customers involved in the process. The result of the SIPOC diagram is not discussed in the article. Therefore, any stakeholders of the process or any external influences are not defined.
SOLUTION METHOD, TECHNIQUE OR PRINCIPLES
Defining the Target System
In defining the target system, the team uses the SIPOC diagram and cross-functional process flowchart to determine the scope of the project. As mentioned earlier the SIPOC diagram is used to identify the suppliers, input, process, output, customers, and any stakeholders involved in the system. SIPOC helps the team to recognize the impact of changing the process has on all individuals involved.
The cross-functional process flowchart is used map out the turnaround process more thoroughly. It elaborates on tasks the activities by detailing every step performed. The team primarily uses this tool to prioritize each process. Through using the flowchart, the team identifies the most important tasks and aims to eliminate unnecessary ones.
Analyzing the Current State
In analyzing the current state, the team uses the cause-and-effect diagram, spaghetti diagram, Pareto chart, staff shadowing and delay/problem logs. The results from these charts and diagrams are analyzed by surgeons, anesthesiologists and specialized physicians involved in the TAT process. Since detailed explanation these tools are not provided in the article, further research was done to describe some possible uses for these tools.
Cause-and-effect diagram can be used to identify the causes of increased TAT and delayed FCS. Once all possible cause-and-effects of the situation are laid out, the team can identify the root causes and key issues of the problem. Targeting the root causes and key issues will greatly improve the process.
Spaghetti diagram illustrates the connections between equipments and supplies used in the operation process. The team can use this tool to reorganize the OR in such a way that unnecessary movements can be avoided in preparation of the OR and patients.
Pareto chart can be used to graphically display numerical data for better and easier analysis. Staff shadowing and delay/problem logs provide additional information essential for systemic analysis of the current situation.
Designing Future State
In designing for future state, the process improvement team conducted a Kaizen event to discuss possible ideas and to implement the solutions developed. The Kaizen event consists of a cross-functional team that focuses on reorganizing the work area. The team uses the 5S approach to remove any unneeded supplies and to, overall, improve the material flow around the OR. The 5S methodology uses the steps of sort, setting in order, shine, standardize and sustain to effectively organize the workspace. Effective organization allows for fewer unnecessary movements and better workflow. According to the case study, the Kaizen event resulted in:
* Reduction of total inventory by about $22,000
* Reduction of the physical “foot print” of floor space required in the OR for equipment, instruments, and supplies by 38% * Improvement of accuracy and feasibility of inventory levels * Improvement of layout and flow of case picking area
* Creation of a structured audit process and tool to monitor and sustain the 5S system of organization (Glover, et al).
As part of the sustainability aspect of 5S, a meeting is held at least every 2 weeks to evaluate the current situation and the progress made with the Kaizen event.
UTILITY OF THE SITUATION
Implementation considerations, i.e., possible issues related to the environment such as ethics, regulations, politics, financing, culture, that need to be considered for implementation
For this particular case, there are many implementation concerns that need to be taken into consideration before the actual implementation itself. If some of these factors are not accounted for, then the implementation may not be successful and such factors could be detrimental to any improvement. External factors relating to the environment such as regulations, financing, and culture would all be applicable to this particular case study.
Regulations would be a factor because there might be certain government regulations about where things must be set up in an operating room, and how sterile they must be kept. This case study utilized a 5S improvement event to reorganize the operating room. It is essential that the team keep in mind any regulations regarding how close items can be located to the operating table, and if certain items are not allowed to be in an operating room. For example, if the team wanted to tape off certain areas to designate where machines or supplies should go, they must consider if there are any regulations that might restrict certain types of tape of paint in an operating room.
Another issue related to the environment would be the issue of financing. This issue was somewhat addressed in this case study, especially in the fact that the team made sure to perform the 5S event on a Friday and Saturday when it would not interfere with daily work, which could have ultimately been a major deterrent to the project. The case study did present some of the savings they were able to achieve through the 5S event. However, they did not do a good job of justifying the cost to the project or how it would be financed. The case also presented a pay-based incentive for making improvements, but did not explicitly address where that money for incentives would come from. This is a very important issue that should be addressed, because that money for incentives needs to be financed from somewhere.
Lastly, the issue of making cultural changes is one that needs to be taken into serious consideration. In this particular case study, it is presented that the operating rooms currently feel that they are operating as quickly and efficiently as they can. This means that the clinicians probably do not feel a strong need to make changes, and any change to the culture and system would result in significant resistance if not done eloquently. For example, in this study the issue of surgeon preference and the hierarchy is a cultural issue that must be considered. In an operating room, the surgeon is often the one with the most influence in power, and might feel that their opinions should matter most in the improvement project. This culture aspect must be considered so that any changes made will not offend or cause any additional disturbances in the operating room. The issue of culture at a company is a touchy one if changes and improvements are to be made, but it is essential to take into account and come up with the best strategy for implementing improvements in a system.
Effectiveness of the proposed solution
Overall, the proposed solutions and improvements were met with mixed results and there is room to improve for the solutions proposed in this case. A lot of the positives came from the fact that clinicians were very involved throughout the entire improvement process, and the staff involved in the project were actively engaged from the start. This allowed the staff to see an improvement project from start to finish, and they were also actively involved as stakeholders in the project. From this perspective, the solution was essentially very effective at teaching the staff about possible process improvements, and allowed them to utilize tools that could be effective for them to use in the future.
On the contrary, early assessments suggest that the pay-based incentive towards making improvements was not as successful as they hoped. The data suggests that any incentive had little to no impact on performance in the operating room. In the first two weeks that the incentive plan was implemented, the turnaround time (TAT) and first case start (FCS) showed no improvement. This could be due to the fact that the project was in the early stages, but nonetheless zero improvement in these times is a troubling statistic. The lack of improvement from baseline measures could also suggest that the pay-based incentive for improvement was not sufficient on its own to support improvement. The operating room was likely functioning at a high level prior to the improvement project, and general, systematic inefficiencies were what was holding back any improvement. It was once these systematic issues were addressed that true improvement was achieved.
Once systematic issues were attended to, both the TAT and FCS showed improvement. After systematic improvements from a Kaizen event and 5S, the FCS showed an improvement of roughly 25% after implementation. The improvement shown can be attributed to changes made in scheduling and facility layouts in the operating rooms. Additionally, a smaller improvement of about 5% was shown in the turnaround time. It should be noted that great improvements were seen in individual teams of surgeons and nurses who displayed a greater sense of commitment to improving their TAT. The improvements in this aspect could have been better sustained, and measures should have been taken to ensure that all surgical teams were committed and onboard to the improvement project.
Drawbacks of the solution methodology
The solutions proposed and implemented for improvement were not without any drawbacks or shortcomings. One of the most glaring drawbacks had to do with the pay-based incentive towards improvements made. This essentially was meant to provide a financial reward to the surgical teams that embraced improvement strategies to improve their turnaround time and first case start time. Using financial incentive like this are not always unsuccessful, but usually they are not the best strategy to use to motivate improvement. In this particular case, many of the operating rooms were already functioning at optimal timing, given the circumstances of the organization and current system. It is very likely that many of the surgical teams felt they were performing as best as they could, given their current resources.
CONCLUSION
Discussion of alternative ISyE tools that could have been used (if there exists any)
A wide range of industrial engineering tools were used in this case study, but there are a few that could have been used, and even added to the success of the project. We both worked on a 5S improvement project at UW-Hospital and utilized a few different tools that could have been applicable in this case study. One thing that this case study did not utilize much were questionnaires, interviews, or focus groups to discuss the project before implementation. These are all effective tools to use before starting a project, and can really help to ensure that the staff’s desires are reflected in any changes that are being proposed.
Another industrial engineering tool that could have been used in this case study is the tool of simulation. Much like simulation was used for an emergency room improvement project. A simulation model of the operating rooms could have been built and utilized before the actual project was implemented. For example, the model could have been used to show how certain improvements in the layout and organization would have affect the turnaround and first case start times. This simulation could have provided added motivation and support to prove that the implementation of the plan was going to be useful.
Overall evaluation of the study
We believe that this case study presented a fairly effective implementation and solution plan to improve efficiency in an operating room. The metrics to improve upon were carefully chosen and provided an opportunity to show true improvements. Additionally, the study utilized many tools and did not have too narrow of a focus. The case study also effectively used teamwork, but the motivation behind improvement was lacking. The study could have done more to show how the improvements might affect the performance of the surgical teams. This case study proved that pay-based incentives alone are usually not enough to motivate workers to change, and other systematic inefficiencies should be coupled with pay-based incentives. The case study also slightly lacked in accounting for some environmental factors such as financing and cultural change. These aspects could have been better accounted for.
The specific 5S project was performed well, and made sure to address the final S in sustain which is often times the one most overlooked, but essential to ensure that the progress made is not lost in the future. They made sure to have bi-weekly meetings after the 5S event, and supported the teams after improvements were made. Having performed a 5S improvement project ourselves, we found both similarities and differences that contributed to the success of this case study. Overall, the improvement in first case start time was notable, but the improvement in turnaround time was minimal at best. In conclusion, we believe that the study could have made use of additional tools, and taken into account additional factors to improve upon their success.
References
Glover, Wiljeana J., Eileen M. Van Aken, Kevin Creehan, and John Skevington, II. “Glover, et al on Using Lean Principles to Improve Turnaround Time and First Case Starts in an Operating Room.” Society for Health Systems Conference and Expo (2009). Print.
Ahlostrom, Janice. “Using the 5S Lean Tool for Health Care.” http://www.wipfli.com/resources/images/5024.pdf (March 2007). Online.