Juran Trilogy
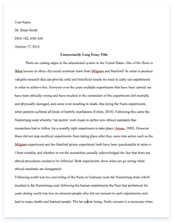
- Pages: 21
- Word count: 5092
- Category: Management
A limited time offer! Get a custom sample essay written according to your requirements urgent 3h delivery guaranteed
Order NowWith the dawn of the Industrial Revolution at the turn of the 19th century, the threat of war, the Great Depression, some manufacturing companies were looking to increase production rates, thus hoping to increase their overall profitability margins. Many challenges were faced by these companies through these difficult times and some leaders offered ideas and solutions that they hoped would help solve some of these grave concerns. Dr. J M Juran was one of these great scholars, whose ideas were centered on Total Quality Management in the modernization effort of the workplace. He believed that improving the quality output of a product to the consumer would increase the profitability rate back to the companies and thus reduce downtime at the manufacturing plants. We will research his contribution towards this goal.
Introduction
Several leaders of the early 19th and 20th centuries had many different visions and views on how to increase production throughout the assembly plants. Dr. J M Juran was one of those pioneers who believed in employees, sought to change ways that products were manufactured, identify problems within the plant site and create solutions to resolve stumbling blocks thereby increasing morale, productivity and profitability. He was the first to think about the cost of poor quality, as was illustrated by his “Juran trilogy”, an approach to cross-functional management, which is composed of three managerial processes: The underlying concept of the quality trilogy is that managing for quality consists of three basic quality-oriented processes.
Quality Planning.
Quality Control.
Quality Improvement.
Each of these processes is universal; it is carried out by an unvarying sequence of activity. Without change, there will be a constant waste. During change there will be increased costs, but after the improvement, margins will be higher and the increased costs get recouped.
Biography-Joseph M. Juran
Joseph M. Juran was born December 24, 1904 and died February 28, 2008. He was a 20th-century management consultant who is principally remembered as an evangelist for quality and quality management. In Juran’s early life, he excelled in mathematics. He graduated from Minneapolis South High School in 1920 and then in 1924, he received a bachelor’s degree in electrical engineering from the University of Minnesota .He then joined Western Electric’s Hawthorne Works. This is where he got his first job troubleshooting in the Complaint Department. In 1925, Bell Labs wanted all Hawthorne Works personnel to be trained in statistical sampling and control chart techniques. Juran was then chosen to join the Inspection Statistical Department, a small group of engineers’ in-charge of applying Bell Labs’ statistical quality control innovations. This is the job that started his whole career. Juran was promoted to Department Chief in 1928, and the following year became a Division Chief. In 1937, he moved to Western Electric/AT&T’s headquarters in New York City.
Around this time the Great Depression was on going. He returned to school at Loyola University Chicago School of Law in 1931. He graduated in 1935 and never worked in law again. During the Second World War his employer got Juran a new job working in the Lend-Lease Administration and Foreign Economic Administration. Just before war’s end, he resigned from Western Electric with the intentions to become a freelance consultant. He then became a professor of industrial engineering at the New York University. He also worked at a small management consulting firm on projects for Gillette, Hamilton Watch Company and Borg-Warner. After the firm’s owner died, Juran took over this firm until he retired in the late 1990s. Once the second world war ended Japan was making products that were not of quality and because Juran wrote a book called Juran’s quality handbook in 1951 the Japanese industry leaders became interested in Juran and invited him to Japan to help them with the quality of the products being made.
When he finally arrived in Japan in 1954, he visited 10 companies. He taught companies that they need to be trained from management down and it took Japan 20 years to catch on. During his life, he made ten visits to Japan, the last in 1990. Once the USA saw Japan’s success they followed in their footsteps. (joseph M. juran) Juran also made many contributions some of which were “The Pareto Principle”. In 1906, Italian economist Vilfredo Pareto created a mathematical formula to describe the unequal distribution of wealth in his country, observing that twenty percent of the people owned eighty percent of the wealth. In the late 1940s, Juran inaccurately attributed the 80/20 Rule to Pareto, calling it Pareto’s Principle. This principle can be a very effective tool to help you manage effectively. He also contributed to management theory. Management theory was a principle that focused on the quality at the end or finished product. The tools used were sampling, inspection plans and control chart.
Juran is credited for adding the human side to this theory created by Pareto. Juran pushed for education and training and he thought that dealing with the change was going to be the hard part of this theory. He also made The Juran trilogy-the cost of poor quality. This was the first approach to cross-function management, which is composed of three managerial processes: quality planning, quality control and quality improvement. The Juran trilogy was about planning, educations and continuous improvement but evaluating. As stated above Juran retired in 1990, but work did not stop. He was still active well in to his 90s and only gave up traveling internationally at 86. In Juran’s retirement he still gave interviews, consulted for western European and Japanese companies such as Xerox and Rolls-Royce, Volkswagen, Toyota Motor companies and many more. Juran also founded the Juran institute and wrote many books such as Quality Control Handbook, Managerial Breakthrough Management of Quality Control, Quality Planning and Analysis, Upper Management and Quality, and Juran on Planning for Quality. (joseph M. juran, 2012)
History of TQM
Total is something that makes a whole, quality is the degree of excellence that a product or service provides and management is the act or art/, manner of handling controlling and directing it. Quality can be found looking at the pyramids in Egypt. Today we can trace quality back to the 1920s when statistical theory was first applied to quality control. To get products of quality it takes effort, specific theories, inspections and production management. Now we’re going to take a walk through time and discuss a little bit about the history of quality and where it started and where we are today. 1800
In the 1800’s when manufacturing of products were produced in small quantities, owners only used inspection. Inspections were used to decide whether a worker’s job or a product met the requirements. It was not done systematically but worked well for small volumes of product being produced. 1911
In 1911 organizations and production levels got larger and needed a new way to manage. Frederick W. Taylor began to look at individual workers and work methods. The result was Time Study and standardized work. He called this Scientific Management. Scientific management was used to improve economic efficiency, especially labor productivity. Frank Gilbert added Motion Study and Process Charting. Process charts focused attention on all work elements including those non-value added elements which normally occur. 1920
In 1920’s statistical process control was applied to quality control to seek and fix problems and make better quality products. Dr.W.Shewharts (grandfather of TQM) developed the statistical methods, one of which were the modern control charts that were used to track and show problems in production so he could find a solution to the problem. Statistical process and quality control focus on the product and finding and controlling quality problems. It should be carried out in stages and relies on trained production personnel and quality control professionals. Stewart’s work was later developed by Deming (made the 14 points which provides theory for management to improve quality) and Juran (efforts on quality involvement in all levels and sectors of management) but not really used until the 1940’s 1940s
In the 1940’s Japanese products were considered cheap and not of good quality. A lot of industries leaders noticed the quality of their products and wanted to fix it so they invited some professionals to help with this problem –Deming, Juran and Feigenbaum. Deming told the Japanese that it would take 5 years to implement the plan but the Japanese didn’t believe him or the other professionals but followed their advice anyway. They gained success in producing quality products and never looked back. Ten years after in the 1950s quality control and management developed quickly and became the new era for Japan. Quality didn’t just stop at management; it went right through to the workers. Devoted workers made up groups called quality circles and in the 1960s were groups of volunteer workers who meet and discussed ways to improve quality. The effect of these groups was wonderful causing an employee movement. Workers felt motivated and involved so this not only improved the quality of products but the quality of the whole organization. This was thought of as the real start to total quality. Total quality in terms was first heard of in paper by Feigenbaum at the First International Quality Control Meeting and its term covered a lot of organization issues. In Japan the term meant companywide quality control from worker to management where everyone played a big part in an organization. 1980- 1990
1980s to the 1990s a new begging came called total quality management (TQM).Western countries saw the success of Japan so they followed in Japan’s footsteps by creating their own quality incentives and quality became the new focus for western countries. In 1988 we took a big leap forward when the Malcolm Baldrige award was first introduced to the USA. The model was the first internationally recognized TQM model. In 1992 the Europeans created a model just like the States. While major companies competed to win the award, the main purpose was to encourage companies to take on quality management principles and to measure where they are and where they want to be. Today, an increasing number of organizations, large and small have become total quality management leaders. We have business excels model which are similar to the TQM model just more clearly defined. Therefore, we can trace quality back from the pyramids but over the years quality in organizations has grown and changed our way of thinking. It does that with a lot of planning, effort, specific theories, inspections and production management. Quality is better now than it ever was and is still getting better but without a beginning we probably would have never started. (History of Quality , 2002)
Contribution to Industry
Juran is one of those rare individuals whose contribution to society equals the most elective work spans generations to make a contribution by anyone in the recent century. His ground breaking works in quality, his inspiration and instruction were all used in a practical management and leadership way. They were catalyst ways that have been applied by many institutions. One of his contributions to the industry was the Juran Trilogy, also known as The Quality Trilogy, a universal approach to quality which is an approach that takes into account the various product lines etc. The Trilogy is an effective way to get top management involved in the quality management process. Ultimately, the quality is top managements responsibility. (the juran quality program-wetherhaven, 2005) Trilogy is the strategic reasoning that explains why all these tools and steps are necessary. Specifically, the Juran Trilogy is comprised of three major stages—Quality Planning, Quality Control, and Quality Improvement. These three stages, taken as a whole, form the basis for the entire quality management effort.
All three processes are universal and could be applied to a particular process, product, internal or external customers, etc. Further, these processes could be performed by top management or by middle management. For example, top management could determine overarching quality goal. These and other goals then would be deployed throughout the organization. Middle managers and operating forces then bear the main responsibility to translate those quality goals into sub-goals, pertaining to the respective functional processes and activities. At times, middle managers could undertake initiatives for quality improvement, without being directed from above. In any way, the universality of the Trilogy makes it an effective and appealing model for significant quality improvements. (Pradeep, 2009) Quality planning is the first stage of the Juran Trilogy and is essentially concerned with designing products and processes that align with customer needs. According to Juran, quality planning is comprised of the following steps: 1. Determine who your customers are. Where customers are numerous, customers should be segmented using the Pareto principle. This allows you to place more of your planning emphasis on your most important customers. 2. Discover your customers’ needs.
Keep in mind that your customers may have needs that they do not voice explicitly. 3. Develop products whose features align with the customers’ needs. Utilize tools such as Quality Function Deployment—also known as the House of Quality—to translate customer needs into product specifications. 4. Develop processes that are capable of producing these products along with their accompanying features. 5. Hand these plans off to operations. Often this entails an abrupt transition of responsibilities as the quality planning team The second stage of the Juran Trilogy is Quality Control. After the planning team hands its plans off to operations and production begins, the firm should simultaneously take steps to ensure that its operations maintains the level of quality that was planned for. This is the purpose of quality control. Quality Control is a universal managerial process for conducting operations so as to provide stability-to prevent adverse change and to “maintain the status quo”
According to Juran, quality control is comprised of the following three steps: 1. Evaluate actual operating performance. It is important that you know what to measure; for example those dimensions that are important enough have operating goals attached to them. Statistical tools are very useful for evaluating operating performance. 2. Compare actual performance to operating goals. In addition to merely comparing, you should again use statistical tools to interpret the meaning of any differences between performance and goals. 3. Take action in response to differences. Because your operating goals should be based on your processes’ capabilities, you should find that any differences between performance and goals are merely sporadic and attributable to unique, identifiable process breakdowns. Often the corrective actions for such problems are as simple as replacing a worn-out part or re-adjusting a machine component. Quality control can also be described as “a process for meeting the established goals by evaluating and comparing actual performance and planned performance, and taking action on the difference”. (joseph M. juran) Quality improvement is the third and final stage in the Juran Trilogy.
Improvement goes beyond control in that it allows the firm’s operations to reach levels of quality therefore unattainable. The quality improvement process does this by removing the chronic quality problems that were built into the products and processes in the planning process. Additionally, the organizational learning that occurs during quality improvement efforts—the “lessons learned”—should be taken into account and utilized, where applicable, in future quality planning. According to Juran, quality improvement includes the following steps: 1. Establish the infrastructure needed to facilitate continuous quality improvement. This step should include the formation of a standing Quality Council whose responsibility it is to ensure that quality improvement efforts receive sufficient attention, effort, and resources. 2. Identify specific improvement projects. The Quality Council should consult employees, customers and cost-of-poor-quality data in identifying potential projects. 3. For each project, establish a team that is clearly charged with the responsibility of bringing a successful resolution to the project. 4. Provide project teams with the necessary training, resources, and motivation to successfully complete the project.
The Juran Trilogy Diagram: The three processes of the trilogy are indicated in the diagram, which is a graph with time on the horizontal axis and cost of poor quality on the vertical axis. The planners are responsible for the product and process design to meet the customer needs; and the job of the operating forces is to run the process and produce the products. We will see that the process cannot achieve 100 percent quality if 20 percent rework has to be carried out. Quality control prevents the situation from getting worse and avoids putting off the fires, such as the sporadic spike. In due course we will see that the chronic problems have come down by the application of the quality improvement process. From this diagram it is clear that quality improvement reduces quality issues but in order to sustain the new level there must be improvement in the quality planning process. (Pradeep, 2009) Juran worked long and hard on this Trilogy he overcomes many strengths and weakness while doing so some of these were: Strengths
The methodology searches a continuous improvement of quality in every aspect of the organization, because if the implementation of the methodology does not give the desire results it is possible to start all over again as the methodology allows the use of different quality tools to cover the steps of Juran’s Trilogy. It allows a better understanding of the relationships at every stage of the company as the methodology is well structured which allows the companies that implement it, an easy understanding and application.
Weakness
To have quality control it is necessary to have a trained person with knowledge in statistical processes or train a special person to be in charge of quality. The program focuses on the company process and not on the labor force. Analyzing the requirements of the program, we found that the companies who apply the program have a complex level of organization. These methodologies show results in the long term; which, in turn represents a risk for the company because the implementation of the quality program can be a waste of time, money and resources. (juran & Deming) The Juran Trilogy was used by many companies and was proven successful. Juran made many contributions to the field of quality management in his 70+ active working years.
His book, the Quality Control Handbook, is a classic reference for quality engineers. He revolutionized the Japanese philosophy on quality management and in no small way worked to help shape their economy into the industrial leader it is today. Dr. Juran was the first to incorporate the human aspect of quality management which is referred as Total Quality Management. The process of developing ideas was a gradual one for Dr. Juran. Top management involvement, the Pareto principle, the need for widespread training in quality, the definition of quality as fitness for use, the project-by-project approach to quality improvement–these are the ideas for which Juran is best known, and all emerged gradually.
Experiments & Methodologies
Test of theories through experiment usually involves producing trial samples of product under specially selected conditions. The experiment may be conducted either in a laboratory or in the real world of offices, factories, warehouses, users’ premises, and so on. It is easy enough to state the “minimal criteria” to be met by an experiment. It should: 1. Test the theories under study without being confused by extraneous variables. 2. Discover the existence of major causes even if these were not advanced as theories 3. Be economic in relation to the amounts at stake
4. Provide reliable answers
To meet these criteria requires input from several sources:
1. The managers identify the questions to which answers are needed. 2. The technologists select and set priorities on the proper variables to be investigated. 3. The diagnosticians provide the statistical methods for planning the experimental design and analyzing the resulting data. Designs of experiments range from simple rifle shot cases to the complex unbridled cases, and most of them are not matters to be left to amateurs. In its simplest form, the “rifle shot experiment” uses a split-lot method to identify which of two suspects is the cause. For example, if processes A and B are suspects, a batch of homogeneous material is split. Half goes through process A; half goes through process B. If two types of material are also suspects, each is sent through both processes, A and B, creating a two-by-two design of experiment. As more variables get involved, more combinations are needed, but now the science of design of experiments enters to simplify matters. (Neuhauser, 2006) In the “unbridled experiment”, a sample (or samples) of product are followed through the various processes under a plan that provides for measuring values of the selected suspects at each stage.
The resulting product features are also measured. The hope is that analysis of the resulting data will find the significant relationships between causes and effects. The unbridled experiment should be defined in writing to ensure that it is understood and that it represents a meeting of the minds. Carefully planned experiments have a high probability of identifying the guilty suspects. The disadvantage is the associated cost and the time interval needed to get answers. Statisticians have developed remarkably useful tools: to get rid of unwanted variables through “randomizing”; to minimize the amount of experimentation through skillful use of factorial, blocked, nested, and other designs; to read the meaning out of complex data RETROSPECTIVE ANALYSIS; LESSONS LEARNED
Lessons learned are based on experience that is derived from prior historical events. These events become lessons learned only after analysis—“retrospective analysis.” An enormous amount of diagnosis is done by analysis of historical events. A common example is seen in quality control of an industrial process. It is done by measuring a sample of units of product as they emerge from the process. Production of each unit is a historical event. Production of multiple units becomes multiple historical events. Analysis of the measurements is analysis of historical events and thereby an example of retrospective analysis. (jurans quality trilogy) The Santayana Review. A short name is needed as a convenient label for this process of retrospective analysis. The philosopher George Santayana once observed that “Those who cannot remember the past are condemned to repeat it.” The Santayana review is the process of deriving lessons learned from retrospective analysis of historical events. The Influence of Cycle Time and Frequency. Use of the Santayana review has depended largely on: 1. The cycle time of the historical events
2. The frequency of these same events, which is closely correlated with their cycle time The influence of these two factors, cycle time and frequency, is best understood by looking at a few examples. Typical utility water systems are subject to considerable variation. Makeup water characteristics can change over time. The abruptness and degree of change depend on the source of the water. Water losses from a recirculating system, changes in production rates, and chemical feed rates all introduce variation into the system and thereby influence the ability to maintain proper control of the system. Other variables inherent in utility water systems include:
* Water Flow/Velocity
* Water Temperature
* Process/Skin Temperature
* Process Demands
* Evaporation Rates
* Operator Skill/Training
* Water Characteristics (suspended solids, hardness, pH swings)
* Treatment Product Quality
These variables are considered and introduced during the applications and pilot plant testing of new products for the treatment of various water systems. Pilot plant simulation of actual operational variation is a challenging task. Every industrial water system is unique, not only in the production operations it supports and the sources of water it receives, but also in the degree of inherent variation encountered due to the factors listed above. While a very sensitive treatment program that must operate within a narrow control range may be suitable for one system, another system requiring the same degree of protection may be incapable of maintaining the required control. Consequently, inferior results must be accepted unless the system is improved to support the sensitive program. In operating systems, proper treatment of influent, boiler, cooling, and effluent waters often requires constant adjustment of the chemistry to meet the requirements of rapidly changing system conditions. A well designed program is essential to maintaining proper control. The program should include proper control limits and the ability to troubleshoot problems that interfere with control of water chemistry.
Success in troubleshooting depends on the knowledge, logic, and skills of the trouble-shooter. In order to improve operations it is necessary to recognize the importance of continuous improvement and to be familiar with some tools and procedures necessary to support this effort. Adequate and reliable data are essential if variation in a system is to be measured and reduced. Specialized computer software can assist efforts to manage, summarize, and use data effectively. Process data can be stored in a database and retrieved and analyzed as needed in a variety of formats. Computers provide nearly instantaneous access to many months or years of process data that would require several filing cabinets if stored on paper log sheets. The computer can be used to graph and analyze the data in a variety of formats, such as statistical process control (SPC), trend analysis, and histograms. The operator is able to troubleshoot the system based on these analyses without spending large amounts of time manually researching and analyzing the data. In his classic book Managerial Breakthrough, Dr. J M Duran develops the important distinction between quality control and quality improvement, and describes the elements of effective problem solving in each case.
Contribution to the Safety Field
Achieving high quality in an ever changing continuous process, quality management emphasizes the ideas of working constantly towards improved quality. It involves every aspect of the company’s processes, environment and people. The whole workforce from the CEO to the Line Worker must be involved in a shared commitment to improving quality. Therefore in brief, Quality and Total Quality Management in particular can be defined as directing (managing) the production process to produce an excellent product or service. Total Quality Management differs from other management techniques in the attitude of management towards the product and the worker. Quality is controlled by prevention, example safety. Quality is built in at every stage and safety for workers has become a major player in the quality process. The major quality management principles are: Quality, Teamwork and Proactive Management Philosophies for process improvements which include ensuring the health and safety of all employees.
Joseph M Juran is widely credited for adding the human dimension to quality management. He pushed for the education and training of managers. For Juran, human relations problems were the ones to isolate. Resistance to change or in his terms cultural resistance was the root cause of quality issues and if management were educated and trained in certain areas such as employee’s health and safety this would add to the Total Quality Management and process improvement. Having employees involved in the whole process empowers them to take pride in their work and work processes leading to a safer and more efficient workplace. (Quality,health,safety,enviroment and training) Joseph Juran developed the 10 Steps to Quality Improvements which also applies to the safety for employees. The 10 Steps are:
1. Build Awareness of Opportunities to improve
2. Set Goals
3. Organize to reach goals
4. Provide Training
5. Carry out projects to solve problems
6. Report Progress
7. Give Recognition
8. Communicate Results
9. Keep Score
10. Maintain Momentum by making annual improvements part of the systems and process of the organization
Participative Management is the opposite of Hierarchical Management style of the early twentieth century business. It involves all employees in the management and decision making process by having mangers set policies (example Safety Policies) and making key decisions based upon the advice and ideas of subordinates. This method provides management with more information from the Front Line Workers and motivates them as they have some control of the decisions. (quality and total quality managment) Another area of transformation by Total Quality Management is in human resources. Numerous studies have indicated that human resource practices that improve the corporate culture lead to better profits. Therefore many companies have extended Total Quality Management to the human resources development Dept. Yet another area of development of Total Quality Management is in the area of ethical philosophy and behaviour of Top Management.
Corporate scandals have increased interest from the public in corporate responsibility and accountability. Corporate responsibility is defined as how a company’s operating practices affects its stockholders, employees, consumers, and the natural environment. This new quality movement is being called Total Responsibility Management. It involves responsible visions and values that leadership builds to reach their values and goals. Total Quality Management has contributed tremendously to the health and safety of workers. Health and Safety policies provides employees with a clear understanding of the importance we place on conducting work in a manner that provides for the greatest safety for everyone and assigns accountability for compliance with these policies at the highest levels. All employees perform work in a way that protect and promotes the health and safety of themselves, their co-workers and the public, and that they comply with all applicable health and safety laws and regulations. (joseph M. juran, 2012) Conclusion
Productivity and performance of an organization ultimately depends on the depth and quality of knowledge and skills of its employees. Advancing such knowledge and skills rests on the training and development offered by their employer and taken advantage of by its employees. In accordance with the desire to ensure quality work of employees and to minimize the legal, financial and physical risk posed by insufficient training, each employee needs to be proactively trained which all stems from Total Quality Management. Dr. JM Juran was one of many great gurus of quality management. He had accomplished so much in his life time and he made great contributions to companies worldwide. Because of him and others like him, we are where we are today and thanks to them we will have an even better future.
References
History of Quality . (2002). Retrieved from http://www.bpir.com/total-quality-management-history-of-tqm-and-business-excellence-bpir.com.html the juran quality program-wetherhaven. (2005, june 30). Retrieved from www.wetherhaven.com/~conversation/…/vitalfew-juran-ppt.pdf joseph M. juran. (2012, novermber 22). Retrieved from http://en.wikipedia.org/wiki/joseph_m._juran joseph M. juran. (n.d.). Retrieved from http://www.skymark.com/resources/leadersjuran.asp juran & Deming. (n.d.). Retrieved from www.prismconsultancy.com/comparingdemingandjuran.pdf jurans quality trilogy. (n.d.). Retrieved from http://www.shsu.edu/~mgt_ves/mgt481/lesson13/sld012.htm Neuhauser. (2006, october 15). joseph juran: overcomming resistance to organisatonal change. Retrieved from http://www.ncbi.nlm.nih.gov/pmc/articels/PMC2565827/ Pradeep. (2009, january 19). the juran trilogy. Retrieved from http://www.businessgyan.com/node/5409 quality and total quality managment. (n.d.). Retrieved from http://www.enotes.com/quality-total-quality-managment-reference/quality-total-quality-managment Quality,health,safety,enviroment and training. (n.d.). Retrieved from http://www.lifting.com/company/industrial-quality.htm