Information for Internal Use
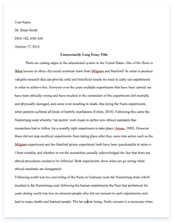
- Pages: 13
- Word count: 3213
- Category: Management
A limited time offer! Get a custom sample essay written according to your requirements urgent 3h delivery guaranteed
Order NowThe mainstream of authors embrace the point that quality circles could have much healthier option of endurance if they were considered as one branch of incessant procedure of TQM. Unluckily a big number of circle programmes over the world in different firms were introducing too early a structure for TQM which was already in position and as a result many of the circle programmes never been a success story. (Langley 2004, p691-711) A problem that is faced by many firms is how to incorporate TQM circles into a course of incessant quality. The rationale of this paper demonstrate that how to inspect the association of circle programmes to current scenario of any organisation, and an awareness of the weaknesses of quality circles and how these can be remedial, as well as the strengths. Further, understanding of the tools and techniques which can be used by quality circles to investigate and remedy quality problems, and demonstrate an understanding of the organizational implications of instituting a programme of quality circles. (Forray and Woodilla 2002, p899-916)
Quality circle at UPS a case study
The Impact of Globalization on Quality Since the beginning of the quality movement post World War II, globalization has had a drastic impact on quality. When the U.S. was the only major manufacturer in the world after the others had been demolished during WWII, the U.S. began producing goods with little concern for quality. Without any competition and the market in high demand, the U.S. prioritized mass production of low-quality goods. Over the next few decades, globalization rose and brought on competition.
The competition came in the form of better quality products and lower costs, which pressured the U.S. to change its strategic approach toward quality in order to regain its competitive edge. In addition to increased competition, globalization has brought awareness among consumers of their demand for higher quality products and services, product availability, and price research. (Floyd and Lane 2000, p154-78) Technology advancements and the internet have increased the amount of information available to consumers and businesses alike whilst making it easier and faster to communicate, especially over long distances. Consumers are able to research the product in terms of quality and prices. Organizations that conduct business overseas have to ability to communicate almost instantly with its foreign subsidiaries regarding the supply chain, inventory, and production. (Lounsbury et al 2003, p71-104) Whilst specific approaches to quality improvement depend on the situation, certain guidelines can be helpful:
1. Quality improvement must not be a fad; it must be a long-term, continuous effort. There are always opportunities for improvement.
2. Whilst top-management commitment is of vital importance, everybody in an organization, from top to bottom, must be committed to quality.
3. Most quality problems require the cooperation and coordination of many functional departments: production design, testing, engineering, manufacturing, marketing, and so on. These problems must also be the concern of labour and management.
4. Ideas and suggestions for quality improvements can come from many, often unexpected, sources. Tap ideas from the most important resource: people.
5. Quality control should be done at crucial steps in the operations process. Set quality criteria for each important step. It is not enough to test the product at the end of an assembly line, for example. If a problem develops, fined the underlying cause; ask why something went wrong.
6. A quality improvement plan is not enough. Provisions must be made for its implementation.
Overall, globalization developed a need for TQM, continuous quality improvement techniques, all of which emphasize the need for competitiveness in a global market. In the traditional style, employees lack the freedom to be creative in their work and are to follow specific instructions or processes without thinking. (Langley 2004, p691-711)This style of management often looks to the employees as the problem. Unlike the traditional style of management, quality-focused management encourages its employees to be creative and resourceful, which can develop a sense of employee ownership and empowerment. The quality-focused style of management also promotes the use of teams to brainstorm and focus on meeting objective together. In this style of management, a surfacing problem is viewed as a problem in the process, and not the employees. (Vaara et al 2004, p1-36)
Quality-focused management is necessary for TQM because that style places emphasis on improving the process whilst striving to understand and satisfy the needs of the consumer. Fitness For use: In this case a customer will consider the features of a product or service and factors such as convenience or ease of use, the style, durability, and reliability. These all play a big role when a customer assesses fitness for use. Support: Warranties, guarantees or after sales service are the additional features that come with the majority of our products. If the advertisements for a product are misleading then people do not really have faith in the product and may decide against purchasing it or even recommending it to any one else. (Langley 2004, p691-711) People perceive a product even according to its psychological impressions, which include atmosphere, image and aesthetics. In our technical product lines product quality is also judged on the basis of the knowledge and personality of sales people. Continuous improvement is also a very popular management theory that has emerged. In that it supports TQM in many ways. Our company must keep itself up to date and try to improve its manufacturing and other such factors continuously or risk lagging behind and a competitor gaining the edge that was previously possessed by our firm. (Wilson 2003, p225-39)
Increased quality
Through continuous improvement our product distribution gets better and better thus giving our firm a continued competitive edge over our rivals in the industry/market. Decrease in waste. Improved motivation of work force- Higher productivity and increased profits may also bring a reduction in costs thereby increasing profits. These profits may be shared by distributing bonuses among employees thereby motivating them to work harder. (Maznevski et al 2000, p473-92)
Reductions in need for large-scale capital investment
The people we service are the most important asset and they are the ones who should be encouraged to contribute ideas to improve our service process. It is not necessary for effective implementation of large scale investments be made. Increased competitiveness- When our firm improves in service and quality, this will give the firm an edge over its competitors which will be hard to imitate. (Langley 2004, p691-711)
To effectively implement the theory of continuous improvement
We will require a motivated and well trained work force – the workers must be committed to the theory and the company’s mission. They must also have the ability to understand their roles and have the ability to complete their tasks effectively and efficiently. (De Wit B and Meyer 2004) Employees must be able to communicate effectively, suggestions to superiors, and other relevant employees. Security of jobs must continue to be established, in that, workers will not suggest process improvements, if their jobs are threatened by these improvements. We must each understand the whole process, so the managers can organize, control, and plan, and so workers can try to meet the needs and quality requirements of the consumers, within the organization. (Hendry and Seidl 2003, p175-96)
These recommendations will only work if there is a committed management and work force team. Every team must believe in the integrity and ability of the other teams and co-operate and co-ordinate their activities with each other to help implement these recommendations effectively. Some suspected challenges in the implementation of UPS TQM process, if accepted, may be contributed to wrong implementation or targeting small and trivial problems rather than tackling the few but important problems that can actually be well worth it if targeted properly. (Hambrick 2004, p91-98)
If employees are low on morale and the organization, instead of increasing their morale, actually lay down targets that are harder to achieve then morale will reduce even further and there a large amount of adverse effects to follow. Therefore, a high morale workforce will be an essential element of UPS TQM. Another problem is that companies try to solve all problems at once causing confusion and low success rates in minimizing the problem. (Denis et al 2001, p809-37) Our firm must tackle its problems one at a time to avoid this situation. Sometimes, the problem is not only with the teams or the wrong implementation of TQM but with the middle management. (Cummings and Wilson 2003, p16-25) This could affect our ability to meet budgeted targets and threaten jobs. TQM application can be quite feasible for our organization if it is implemented the right way. Effective TQM implementation focuses on customer satisfaction, employee involvement and continuous improvement. Most of our TQM gains will not be radical, but more incremental, meaning that changes will not come about suddenly and in a big way. (Clark 2004 p607-27)
They are more likely to be small but effective. UPS strategists must be patient because it may take a couple of years after effective implementation for financial benefits to set in. In conclusion, the implementation of a UPS TQM will be very effective if implemented well. If we look into the mistakes we make in implementing TQM and measuring our pre -TQM and post-TQM statistics, we may actually notice small but significant changes. Empowerment of employees Apart from being a customer-focused company, UPS also places great emphasis on its employees by constantly motivating and training them, as well as creating a healthy and pleasant working environment demonstrated by its effective promotion from within policy, first name basis communication style, and open door policy. (Vaara 2002, p211-50)
Tools and techniques
As we have mentioned before, The United Parcel Services places high regards to its customers and are constantly monitoring their changing demands and expectations. They acted on this commitment by being the first delivery company that has developed a tracking system. (De Wit B and Meyer 2004) This tracking system benefits the customer by insuring that their delivery will be quicker and more efficient. It also allows customers to locate their packages by entering a twelve-digit number into the UPS website at all times during the delivery. Further technological advances have brought quality of services to customers to a whole new level as was discussed in the technology section. The handling of packages is also a major part of focus on the customer. (Chow et al 2004) Employees are instructed to use a hand to surface method of handling the packages. This type of handling decreases the amount of damage that is caused in route. When loading 18-wheelers with packages, employees are instructed to build walls with matching boxes and to fill in between each wall with more packages to secure the load during transportation. This type of handling ensures a quality of service that benefits the customer. (Lynch 2005)
Measurement is another attribute of Total Quality Management. In an interview with frontline manager at the local Hattiesburg UPS centre, Roger Cooksey, he said that the primary use of measurement for UPS is the internal auditing system. This is a process where auditors come from the main office and physically rate the quality of performance and service of that local centre. Managers are required to fill out a questionnaire of 300 questions for the auditors to evaluate. Areas subject to evaluation includes package handling methods, driver safety, loading methods, unloading methods, routes, truck maintenance, and management. (Hendry 2000, p955-77)
Strength and remedies
In relation to internal effectiveness, there are four management strategies. They are Status Quo Strategies, TQM Strategies, Reengineering Strategies, and Mission Institutionalization Strategies. (Mintzberg et al. 1998)
The vertical axis in figure 1 again is ? measure of increasing focus on the missions and corporate goals; whereas the horizontal axis is ? measure of increasing presence of business related processes. An effective firm must concurrently focus on both business processes and goals. Situation SQ depicts the need for status quo strategies, where goals and processes are properly aligned. (Creed et al 2002, p475-96) This is the position business should endeavour to obtain.
The situations along the diagonal line depict the need for TQM strategies, where some fine-tuning of the processes is needed for better position of corporate strategy and processes. Quality is not only measured by simply customer satisfaction anymore, the company wants more, and it wants to have customer delight. Until recently, it has brought customer management to a whole new level by offering a service for preferred customers. (De Wit B and Meyer 2004) Preferred customers are high volume shipping and receiving commercial customers. Preferred customers can ship at a discounted rate because they compose nearly half of UPS’s total business. As an integral part of the program, Preferred Customer Associates work to ensure a higher level of problem resolution by answering questions and handling concerns for Preferred Customers on a timely basis. (Balogun and Johnson 2004 523-49)
In addition to resolving problems PCA’s also inform Preferred Customers about UPS products and services when an opportunity presents itself.” The extra effort towards these customers is what sets UPS apart from other package and delivery services. UPS also helps the customer in the community not only in the business aspect. They are a large contributor to The United Way. They also have huge disaster relief programs that they integrate into the workplace. Employees are encouraged to help their community in any way possible. UPS also understands the importance of its employees, therefore it provides training and empowers to its employees in order to satisfy the customers. The implementation of TQM has lead to the success of the UPS, and obtaining a lot of awards from recognized magazines and consulting firms. (Wright et al 2000, p807-26)
Additional, quality circle also seek here to make the process themselves more well-organized. These circumstances might occur anyplace along and on either side of the dotted diagonal line. Reengineering strategies are needed when the processes do exist, but necessitate radical transform (as they are not properly aligned with goals). The circumstances could occur anywhere along the horizontal axis. Institutionalization, or formation, of processes is needed even when there are no (or few) processes to hold up corporate missions: we have ? need for better process to hold up the institutional goals. This situation could occur anyplace along the vertical axis. (Knights 2001, p311-40)
Conclusion and organizational implementation
Through our analysis quality circle has observed that circles can be helpful if the organization and quality circles mutually decide the TQM process. But in this analysis we have observed that quality circles were not much successful due to its previous reputation. They company also have methods for evaluating their part-time employees. The pre-load employees are evaluated by the amount of volume that the 18-wheelers carry into the centre. They have a time-chart for how soon the pre-load should be finished according to the volume on the 18-wheelers. The local sort is measured on how fast they can get the packages out. Every person on the local sort must have an average of touching 200 packages per hour. This includes people that do not even touch the packages. (Jarzabkowski 2003, p23-55)
The local sort also containerizes small packages into bags so that the hub will not have to resort them to a new location. They are measured on how many mis-sorts are in each bag. They are only allowed to have one mistake on every 2000 packages without getting reprimanded. UPS is believed to have one of the most elaborate auditing systems around and that all discrepancies are documented and then the E-centre is given a goal list to help increase the productivity as needed. The company is consistently trying to improve on the quality of everything that it does. The major goal of UPS is: every package must be delivered every day. It wants to get every package delivered by the specifications of the customer. If that is a next day early a.m. package, that is when UPS wants that package delivered. Quality circles can be a major part of any organization if circle produce its strength by mutual understanding with firm and its employees.
References
Balogun, J., and G. Johnson 2004 ‘Organizational restructuring and middle manager sensemaking’. Academy of Management Journal 47/4: 523-549.
Chow I, Holbert N, Kelley L and Yu J, (2004), “Business Strategy – An Asia Pacific Focus”, 2nd Edition, Prentice Hall.
Clark, E. 2004 ‘Power, action and constraint in strategic management: Explaining enterprise restructuring in the Czech republic’. Firm Studies 25/4: 607-627.
Creed, W. E., M. ?. Scully, and J. R. Austin 2002 ‘Clothes make the person? The tailoring of legitimating accounts and the social construction of identity’. Firm Science 13/5: 475-496.
Cummings S and Wilson D (eds), (2003), “Images of Strategy”, Blackwell, p16-25.
De Wit B and Meyer R, (2004), “Strategy: Process, Content, Context”, Prentice Hall
Denis, J-L., L. Lamothe, and ?. Langley 2001 ‘The dynamics of collective leadership and strategic change in pluralistic organizations’. Academy of Management Journal 44/4: 809-837.
Floyd, S. W., and P. J. Lane 2000 ‘Strategizing throughout the organization: management role conflict in strategic renewal’. Academy of Management Review 25/1: 154-178.
Forray, J. M., and J. Woodilla 2002 ‘Temporal spans in talk: Doing consistency to construct fair firm’. Firm Studies 23/6: 899-916.
Hambrick, D. C. 2004 ‘The disintegration of strategic management: It’s time to consolidate our gains’. Strategic Firm 2/1: 91-98.
Hendry, J. 2000 ‘Strategic decision making, discourse, and strategy as social practice’. Journal of Management Studies 37/7: 955-977.
Hendry, J., and D. Seidl 2003 ‘The structure and significance of strategic episodes: Social systems theory and the routine practices of strategic change’. Journal of Management Studies 40/1: 175-196.
Jarzabkowski, P. 2003 ‘Strategic practices: an activity theory perspective on continuity and change’. Journal of Management Studies 40/1: 23-55.
Knights, D., F. Noble, T. Vurdubakis, and H. Willmott 2001 ‘Chasing shadows: Control, virtuality and the production of trust’. Firm Studies 22/2: 311-340.
Langley, ?. 2004 ‘Strategies for theorizing from process data’. Academy of Management Review 24/4: 691-711.
Lounsbury, M., M. J. Ventresca, and P. M. Hirsch 2003 ‘Social movements, field frames and industry emergence: ? cultural-political perspective on US recycling’. Socio-Economic Review 1: 71-104.
Lynch R, (2005), “Corporate Strategy”, 4th Edition, FT Prentice Hall
Maznevski, M. L., and K. M. Chudoba 2000 ‘Bridging space over time: Global virtual team dynamics and effectiveness’. Firm Science 11/5: 473-492. Beverley Hills, CA: Sage.
Vaara, E. 2002 ‘On the discursive construction of success/failure in narratives of post-merger integration’. Firm Studies 23/2: 211-250.
Vaara, E., B. Kleymann, and H. Seristo 2004 ‘Strategies as discursive constructions: The case of airline alliances’. Journal of Management Studies 41/1: 1-36.
Wilson, M. 2003 ‘Rhetoric of enrolment and acts of resistance: Information technology as text’ in Global and organizational discourse about information technology. E. H. Wynn, E. ?. Whitley, M. D. Myers, and J. I. DeGross (eds), 225-249.
Wright, Ch. R., M. R. Manning, B. Farmer, and B. Gilbreath 2000 ‘Resourceful sensemaking in product development teams’. Firm Studies 21/4: 807-826.