Design house partnership at Concept Design Services
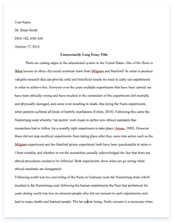
A limited time offer! Get a custom sample essay written according to your requirements urgent 3h delivery guaranteed
Order NowWhy is operations management important in CDS?
Operations management is important in CDS if they are to continue being one of Europeâs most profitable home ware businesses. As with any other company, CDS objective is to add value to their final product while using its resources effectively and efficiently through its internal processes. The company has successfully been able to apply the technology used in the aerospace sector onto home ware items, through the mastering of injection moulding machines. Moreover, the company has expanded into a premium home ware product market, integrating new functions within its operations, such as forming partnerships with reputable designers and increasing the volume and complexity of its production. Draw a 4 Vâs profile for the companyâs products/services Volume: High. Although the case study does not specify the amount of production, it can be deduced that production volume is high as it has increased 600% since the acquisition of new large multi-cavity moulds.
Another indication of high volume production is the fact that CDS decided to subcontract their Focus line to other moulding companies, so they could focus on the production of their premium line (Concept). Variety: High. CDS market is a highly competitive one, in which design innovation determines the longevity of the firm. CDS capacity of developing products that are in fashion and moreover, its adaptability to change as fashion changes is key to the survival of the firm. Variation: High. For the same reason as with variety, CDS is forced to continuously produce innovative designs that would keep their customers interested and therefore keep demand high. Visibility: Mixed high and low. There is the visible part of the operation that is when the final products are What would you recommend to the company if you were asked to advice on improving its operations? There are 2 areas that CDS needs to improve: the relationship between its designers and other parts of the company (such as the manufacturing and distribution) and a better forecasting of sales.
For the first challenge, it seem that the designers donât get to spend enough or any time on the âfloorâ of the company, that is, they do not have an in depth understanding of the manufacturing processes and the way they are affected by their decision making. Perhaps if they could spend some time doing âcross trainingâ they would get a real idea of the manufacturing processes and could implement this knowledge into their designing activities, in other words, both departments should have a better collaboration. The second challenge is improving the sales forecast. Once again there seems to be a problem of collaboration between the marketing and operations departments of the company. As above, it could be suggested that both department managers and key personnel should cross train in order to understand the âway they do thingsâ and the reasons behind them.
New Supply Chain Strategies at Old M&S
Operations Management
About the Business
M&S is a company which was formed in 1884 in Leeds, has become an international group with an annual turnover of over ÂŁ8billion by 1997. M&S experienced a troubling time after 1997 in the market downturn of autumn 1998. Problems
They lost a big chunk of their target market, which was women aged 35-55. What went wrong for M&S was that they only bought substantially for two seasons of the year, autumn and winter and only âphase boughtâ for the rest of the year. Nimbler competitors exploited many more different seasons throughout the year and used this to their advantage. Pre 2000âââSupply chain was too long so long lead times, competitors had higher variety and choicer Post 2000âââRestructuring the supply chain so high costs, implementing the segmentation program Solutions
What they did was that they segmented their clothing into four ranges to give women more variety: 1. The Perfect CollectionâââClassic, stylish merchandise for core customers, 60 lines of clothing including plain, white t-shirts. Easy machine washable and iron able, these were aimed at people with busy lifestyles (working mums for example) 2. The Classic CollectionâââThis range was more aimed at the mature customer by being advertised as comforting, long lasting and versatile. These were high quality, smart and elegant clothes made of the most high quality fabrics 3. The Autograph RangeâââThis was where M&S pulled out all of the stops to attract more customers, bringing in top designers like Julien Macdonald and Phillip Tracey to design clothes and accessories.
The aim of this was to allow the customer to have designer quality merchandise at high-street prices. Only in selected stores though. 4. âper unaâ RangeâââLaunched in September 2001, this range gave customers limited clothing which were deemed very âexclusiveâ and ârareâ and therefore special. The aim of the range was to âprovide superb designs at very affordable pricesâ. The cost of the products was 10% higher than the normal M&S ranges. Made in small batches and scaled down because of the too high customer demand so only in selected stores. Give feedback sheets to customers on what they would like from M&S in the future, so they can continue their flexibility in demand Outsource work to closer places than China to make sure that lead times are reduced and customer satisfaction is high.
4 Vâs of M&S
Performance Objectives
QualityâââWith their new segmentation of product ranges CostâââGood prices for good quality products
FlexibilityâââHaving more varied range of clothes to meet customer demand DependabilityâââMaking sure that lead times are reduced to keep stock high so customers are not disappointed when they get to the store What topics does this case relate to?
Operations StrategyâââThis is due to changing the way they do their operations (for example their supply chain) to make sure that performance objectives are met. SchedulingâââWith the new ranges M&S have had to schedule the times to make sure that items, are on most occasions available and in stock for customers. A good example of this would be their perfect collection as they need to make sure every day, needed items of clothing, like white t-shirts, are always in stock for customers as their target customers are working women Supply Chain ManagementâââThis is with the idea of having Business to Consumer relationships. Also they now use, especially in their per una and autograph ranges, an agile supply chain as there is high variety of products (with the designers) with short lead times. Boys and Boden
Blackberry Hill Farm
Operations Management
About the Business
Blackberry hill farm was a 200-hectare mixed farm in the south of England which changed ownership â15 years agoâ. About the Product/Service
Before
Primarily cereal growing, with small dairy herd, some fruit and vegetable growing. After improvements
Introduced âPick your-own operationâ which turned vegetables and fruit growing from small loss to small profit. Created museum of farming heritage, Introduced tractor rides Organised petting zoo which required new animals to be introduced. Started preserving kitchen started producing 50kg a week, within three months grew to 300kg a week and now producing at 100kg per week. Introduced small adventure playground, cafe, picnic area and bakery. Customer could watch the Jam and bakery as it was âopen viewâ Problems
Before
Needed to rethink management of the farm.
Fruit and Veg were actually making a small loss.
After improvements
Business may not be considered genuine farm due to most profit being made from visitors rather than agriculture. Being a genuine farm is one of their unique selling points that they donât want to lose. If they want to expand further will need to extend the car park which will prove to be expensive Business getting complex to manage, doesnât leave time to think about overall direction. Hard to attract employs since they have to be seasonal due to the business thriving in summer months. Want to increase the revenue while reducing que times.
Solutions
Introduced many new attractions which bought many visitors to the farm making it profitable again. Area devoted to cereals reduced and vegetable and fruit growing area increased- Lean Operations and strategy. Add one more attraction for the year.
Employ some full time staff for the preserves attraction, if it will not affect jamâs shelf life too much. Possible ideas
Develop hedge maze, will require ÂŁ20,000 investment but is believed to bring in an extra 10,000 customers over the summer period. Build of business in organised school visits, will require ÂŁ30,000- ÂŁ35,000 investment for extension on unused farm building, is believed to break even around year two. Link with Lectures
Layout
Each operation will have its own layout strategy; these are some of the main ones Fixed
Pick your own fruit
Exhibits
Petting Zoo
Tractor ride
Process Layout
Farm Shop/Bakery
Cell Layout
Preserving Kitchen
Bakery
Strategy
Added multiple new attractions to bring in new people.
Reduced sections of farm which were not bringing as much revenue as others to allow them to extend favourable attractions. Lean Ops
Ensured that the most profitable parts of the business had room to operate by reducing sections of the business which werenât as popular. Inventory
Have issues whether to introduce more inventory as a result of stock having a earlier expiry date. Forecasting
Used forecasting by tracking the amount of customers that entered the farm, and linked this to product sold and attractions visited. Example they noticed that in winter they had alot of people visiting the shop but not visiting many of the attractions on the farm.
Number of visitors to Blackberry Hill Farm Last Year
Iâll Phone You Back!
Operations Management
About the Business
Oilpartz Ltd specialised in producing some of the larger pipeline components used in rigs, production platforms and on-shore facilities of the oil industry Had some customers from the chemical and heavy engineering industries. About the product/service
Due to the size and complexity of the parts, machining times were long, Dave McDonald normally on orders gave a quoted lead time of six-weeks to complete the operation Dave has around thirty regular customers who valued the exceptional quality and reliability of the Oilpartzâ Partnership. He never accepted orders for repetitive, high volume work
The Background
Dave got a call from Mike Rowlands of Nitro Chemicals stating that he needed 20 small diameter stainless steel rings as soon as possible. Dave had a decision to make: to see if this was possible as he doesn’t like to disappoint the customer when he/she has a request. Dave has four highly-skilled machinists who can do each part of the production process (turn, mill, drill and grind). They work 8 hours a day, Monday to Friday and are willing to do some overtime in evenings or weekends. Although Dave only allows them to do 10 hours overtime a week Dave then after taking some time to go over what jobs Oilpartz are currently working on made his schedules and did account for the request that Mike made him (look below)
How Dave accounted for the scheduling of Mikeâs last minute request. Look at order NC11
How Long NC11 Order would take when you take into account how long it takes to do one of the small diameter steel sealing rings. The 19 x 1.5 part is chosen because 1.5 hours is the time it takes for the longest process to be done.This is flow control Problems
The company has generally quite slow machinery so if the customer wanted a really quick order, the customer could be waiting longer than expected. This affects its dependability and speed. Unexpected machinery failures will make work stop and therefore customers will not get their product on time Solutions
Using flow control to put into his schedules Dave can see that it only 33 hours cumulative work of his workers to get the order done. Which is significantly lower than the other jobs. (look above) Using capacity planning to make sure all workers are working together to make the final product Staggering out each workers overtime. What we mean by this is that if each worker did their 10 hours overtime on different days then this makes causes for 40 hours of productivity to occur as the workers are multi-skilled. What this means that the job could be done in a minimum of 4 days. Use the Just In Time principle where you make sure that each process is done so that it can be quickly moved to the next stage of the production process. So this is Lean How this relates to other topics
Capacity by seeing how much stock/product is needed and accommodating for this Scheduling as you are working out how long it will takes for all jobs to get done on time Quality as Oilpartz use the foundations of Total Quality Management (TQM) to make sure that each customer gets the best service possible. Quality is vital for Oilpartz to make sure relationships between their loyal customers are still in tact. ISO 9000 principle as well-
Trans-European Plastics
Operations Management
About the Business
Trans-European Plastics is one of Europeâs largest manufacturers of plastic household items. Itâs French factory makes a range of over 500 products that are sold to wholesalers and large retailers throughout Europe About the Product/Service
The company despatches orders within 24 hours of receipt using an international carrier. All customers expect their requirements in full within one week of ordering Background Information
The company has 24 injection-moulding machines and weekly promotion schedules are made detailing the sequence of products to be used, the quantity required for each batch and the anticipated timing of each product run The company had fears of encountering some problems which were: Declining delivery reliability, increased levels of finished goods inventor and falling productivity Factory operates on seven hour shifts, Monday-Friday: 105 hours per week of labour for 50 weeks of the year Problems
Because of incredibly high demand for many of its product the backlog of work has to planned 2 weeks in advance, so factory workers need to plan that far back as well They are really struggling to keep several of their relationships with suppliers who expect their requirements within a week There is a massive lack of space in their warehouse due to products being stacked on the floor. This is bad because products can get damaged with forklifts coming along the warehouse. The lack of space would then get filled with backlogs of inventory and then production would have to stop which is detrimental With holding a lot of inventory storage costs are incredibly high, losing out on a lot of money. What did they do/Solutions?
CEO Pierre Dumas stated that âwe have finally agreed to approve an extension (costing over a million euros) to be constructed in June-September this yearâ. This is to combat the lack of space in the warehouse They decided to review all of the re-order quantities so that there is no such occurrences of buying too much stock or too little. Look at the trends in seasonal demand to make sure that they have got products in bulk when they are in their âgolden periodâ (barbecue salad fork are always peak when its in the summer) Links to Module
Lean (Just in Time)âââBy making sure that resources and raw materials are scheduled on time at the start of the week for working to commence straight away. This will allows customers to get their expected requirements within one week StrategyâââTrans-European Plastics make sure they keep to their main performance objectives which are dependability (by getting requirements to the customer within one week) and quality (external perceptions) InventoryâââThis case directly relates to inventory because the company are trying to find solutions to reduce the amount of space taken by unneeded back-stock. Trans-European Plastics I would say currently use a multi-stage inventory system. Changing to a two-stage inventory system will make sure that goods that get to depot are already completed and can go straight to the customer Smart Car
London Zoo
Operations Management
About the Business
· The zoo is located near Regents Park, and opposite a tube station. · Weekends and summer holidays are the busiest periods with regular attendance figures between 4000 and 6000. < Seasonality Aspect! · âVital that we still provide a high quality of serviceâ. · Extensive market research done. The zoo knows the age range, average visit length, travel distance of customers, and favourite animals etc. However⊠(see Problems, bullet point 4) · The zoo doesnât have an issue with marketing, instead they want to organise the operations to give customers a good day out. Naturally if this is achieved than word of mouth and returning customers will be sufficient in ensuring good visitor numbers in the future. · Opened in 1828
· Occupies 36 acres
· Has one of the most prestigious animal collections in the world, including leopards, elephants, giraffes, and gorillas to name a few. · Many various buildings all built and renovated in different years since opening in 1828. (Thereâs a big section on this, but the only relevant piece of information is that all buildings are listed and cannot simply be demolished because of strict guidelines in place).
About the Product/Service
· Various different enclosures with exotic animals, ranging from big cat enclosures to an aquarium. · Petting zoo (opened 1924)
· Catering and face painting both briefly mentioned but are done by franchises, i.e. not directly employed by the zoo. Problems
· Huge fluctuations in daily numbers.
· Xmas particular low attendance, âour lowest budgeted attendance figure is for Christmas Eve with just 48 peopleâ. · Need to increase visitor numbers.
· ⊠âWe do not really know what the public thinks of the quality of the service we provide throughout their visitâ. Big issue considering quality is a main performance objective for the zoo. · Sceptics donât like the thought of animals in captivity and see zoos as a problem rather than a solution. · Over 250 other attractions in Great Britain with animals. In the 1950s there was only 9 other zoos. The result of this is more competition. · Of the various leisure segments, wildlife attractions showed the lowest consistent growth. · Big money problems, even with millions of pounds in grants the zoo still struggles to sustain itself. Solutions
· The special âSave Our Zooâ day had 18,000 visitors! Shows that many people still care about/support the zoo. Maybe more âspecial daysâ could be incorporated, particularly at Xmas where the attendance is especially poor. E.g. âwinter wonderlandâ day with Santaâs grotto, rain deer etc. · Emphasising their commitment to animal welfare and conservation will combat the sceptics about zoos and hopefully provide a better experience for customers. Could introduce ideas like âadopt an animalâ or give talks about conservation to further enforce this. · Recently awarded ÂŁ2 million from the National Lottery Heritage Millennium Fund to go towards building an education centre. ^ Further backs up the previous point. The service quality project
· First of all itâs worth pointing out that this makes up about half the case study. · An MBA student carries out a research project to see how customers rate the service they receive. · The only segment targeted by this project is individuals/families who make up the largest percentage of visitors. · Uses â18 determinants of service qualityâ for the questionnaire. · Questions allow customers to use own perceptions to rate various aspects from 1-5. 1 being poor, 5 being great, 3 being average etc. · These results are then analysed using statistical software. · Questionnaire also asks what customers expected from the zoo, e.g. âI wanted to see a unicorn but you didnât have anyâ. · Completed the questionnaire of various days to make it fair, e.g. on a busy day service may be worse than on a non-busy day. · Used the overall results to devise a prioritised plan of action. NOTE: There is an 8 page(ish) appendix that was handed out in the seminar for this case study⊠if you donât have a copy than itâs probably best to avoid this question because youâll be missing a lot of information.
Implementing lean at CWHT
Operations Management
About the Business
CWHT = Chaswick and Wallasey NHS Hospital Trust.
In July 2011 CWHT took the decision to implement lean thinking across the organisation. CWHT experimented with lean 2 years earlier, but work had been âdisjointedâ, âfragmentedâ, and too focused on optimising departmental targets. To become a total lean organisation, an internal change team was appointed (âlean teamâ) comprising of 11 employees on 2 year contracts. The aim was to move staff out of their functional âsilosâ and to help them see their role within the whole patient pathway rather than within a single function. Lean facilitators underwent training in project facilitation and change management skills. The overall project was set to begin January 2012.
Using the rapid improvement approach
âThe whole point about our approach is fast, focused breakthroughs in performance. You must focus on one true bottleneck and focus on fixing that.â About the product/service
Various healthcare services e.g. A&E
Problems
Lack of continuity with leadershipâââinterim CEO for 2 years, before a new CEO, and new Director of Operations. Performance of A&E only 95%, when it needs to be 98%+ for a good performance rating. Many individuals not convinced that lean can change the organisation for the better, and appointment of new CEO can demotivate staff because it makes some of their previous work redundant.