Decision Making Models
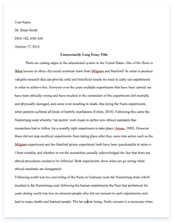
- Pages: 3
- Word count: 611
- Category: Decisions Management Model
A limited time offer! Get a custom sample essay written according to your requirements urgent 3h delivery guaranteed
Order NowThe Economic Order Quantity Model will allow an organization to determine the optimal volume of inventory to order at a given time. The EOQ model provides the most optimized approach to inventory ordering as it considers, demand, ordering cost, and holding costs; to develop the volume of inventory to be ordered to maintain to minimum annual cost (Render, 2012). Equation:
Variables:
Q* = optimal number to order
D = annual demand in units
Co = ordering cost
Ch = holding cost
Process Description:
Q or Q* meaning the optimal order of pieces per order, is equal to the square root of the equation of annual demand (D), multiplied by 2, then multiplied by the ordering cost (Co), which is then divided by the holding cost (Ch). The end result of the equation provides the optimal order of pieces per order or Q*. Company A:
Demand (D) = 670,000 units per year
Ordering Costs (Co) = $320 per order
Per Unit Cost of inventory = $375
Holding cost rate = 5.5%
Holding cost (Ch) = $375 (5.5) = $20.62
*Holding cost is the per unit cost of inventory multiplied by the holding cost rate
Step 1: Input variables into the equation
Step 2: Follow mathematical order of operations: simplify and solve for numerator 2(670000)(320) = 428800000=20795344.3258972 Step 3: Follow mathematical order of operations: Divide numerator by denominator 428800000/20.62
Step 4: Square roots your quotient and get your final result of the equation = 4560 Step 5: Round up to the nearest Unit to get you final answer. In order to minimize total cost, the order size should be 4560 when company A orders new inventory.
B – B1. Economic Production Lot Model
The Economic Production Lot Model is a variation of the EOQ model that allows businesses to determine optimal replenishment lot size. This model provides the most optimized approach this form of ordering as it considers, demand, available production, ordering cost, set up costs, and holding costs to develop the volume of inventory to be ordered to maintain to minimum annual cost (Render, 2012). Equation:
Variables:
Q* = optimal number to order
D = annual demand in units
P =annual available production per year
Co = Production set up cost
Ch = holding cost
Process Description:
Q or Q* meaning the optimal lot size per order, is equal to the square root of the equation of annual demand (D), multiplied by 2, then multiplied by the Production set up cost (Co), which is then divided by the holding cost (Ch) times, demand (D) over production (P) subtracted by 1. The end result of the equation provides the optimal lot size order or Q*. Company B:
Demand (D) = 8,710,000 units per year
d =23,863
Production (P) =148,070,000 units per year
p = 405,671
Production Setup Cost (Co) = $3750 per order
Per Unit Cost of inventory = $190
Holding cost rate = 6.5%
Holding cost (Ch) = $190 (.055) = $10.45
*Holding cost is the per unit cost of inventory multiplied by the holding cost rate
Step 1: Input variables into the equation
Step 2: Follow mathematical order of operations: simplify and solve for numerator and denominator; 2(390000)(425) = 331,500,000; 11.55(1-.59) = 663357.02175647
Step 3: Follow mathematical order of operations: Divide numerator by denominator 331,500,000/10.89 = 499.73089773 Step 4: Square roots your quotient and get your final result of the equation 22.35466166
Step 5: Round up to the nearest Unit to get you final answer. In order to minimize total cost, the lot size should be 23 when Company B orders new inventory.
References
Render, B., Stair, R. M., & Hanna, M. E. (2012). Quantitative analysis for management (11th ed.). Upper Saddle River, N.J.: Pearson Prentice Hall.