Penang Mutiara
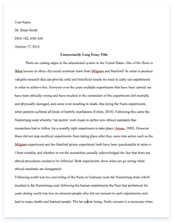
- Pages: 9
- Word count: 2072
- Category: Hotel
A limited time offer! Get a custom sample essay written according to your requirements urgent 3h delivery guaranteed
Order NowTopic Operations Performance: The five operations performance objectives, Also see lecture materials Chapter 2 Hayes and Wheelwrightâs four stages of operation contribution. Topic Operations Strategy: Order winning and qualifying objectives Cost-being productive, quality-being right, speed- being fast, dependability-being on time and flexibility- being able to change. . 1.Quality: Other staffs members can help one and other and make sure they have the correct knowledge. This will save the company testing their employeeâs knowledge. Also the fact that staff members are providing a quality service to customers could potentially increase staff morale because they see that their customers are happy with their quality service and encourages them to keep a high level of quality. If conformance quality is high in all the operations processes and activities very few mistakes will be being made. This generally means that cost is saved, dependability increases and (although it is not mentioned explicitly in the chapter) speed of response increases.
This is because, if an operation is continually correcting mistakes, it finds it difficult to respond quickly to customers requests.2.Speed: Because staff have to give a fast response, this will help maintain dependability as they will be on time. The fact that staff must be able to do more than one job, this shows that speed helps them be more flexible.3.Dependability: helps improve speed internally because they are keeping up with their promises. It prevents lateness causing disruption and wasted time and effort, therefore saving cost and giving an organisation the stability which allows it to improve its efficiencies.4. Flexibility: namely flexibility speeds up response, flexibility saves time (and therefore money), and flexibility helps maintain dependability.5. Cost: If managed properly, high quality, high speed, high dependability and high flexibility can not only bring their own external rewards, they can also save the operation cost Using the Hayes and Wheelwrightâs âFour-Stage Model of Operations Contributionâ analyse the evidence in the case for alternative Stages and then suggest which of these is most likely stage for the Hotel.
Topic: The Strategic Role and Objectives of Operations. Hayes and Wheelwrightâs four stages of operation contribution. Overall, it is probable that the Hotel is a stage 3 organisation. This rating is appropriate as there is mixed evidence in the case study for indicate stage 2, 3 and 4. For stage 2 Wernie may be just copying the best practice he has learnt from working in other luxury hotels. On the other hand there all the indications that there is a clear understanding of how different performance objectives can work to achieve the strategic objective of impeccable customer service which one would expect for a stage 3/4 operation. The evidence for stage 4 is the high number of guest who return (around half the guests have been before) which indicates that the hotel standing stands out as being one of the best in the competitive market that exists for resort luxury hotels. Assertion need to be backed up by quoting evidence from the case. Better students will note that all the evidence in the case is from Wernie so there is every chance of claims being exaggerated. 1bEvaluate what are the Order Winner and Qualifiers for customers of the hotel. Analyse how each of these performance objectives interrelate to achieve the Order Winner while at the same time reducing costs using appropriate examples from the case.
Topic: The strategic role and objectives of operations: Operations performance objectives. The order winner is exceptional personal service quality. Qualifiers are other aspects of quality that one expect in a five star hotel, dĂ©cor, food, rooms etc, and prompt and dependable service. Price can be higher than competition but not excessively so. Internal performance objective that help to achieve the order winner are: Mix flexibility, is illustrated by the multi-skilled workforce that helps achieve dependability and service speed for guests while giving the internal benefit of better staff capacity utilisation for the hotel. Product flexibility achieves quality objective and is demonstrated by the âwe never like to say noâ policy in meeting guestsâ requests this pleases guests but through allowing hotel staff to show their initiative increases motivation.
Volume flexibility allows speed and quality objective to be maintained and is shown in the way the hotel deals with seasonal fluctuations by using temporary part-time staff in backroom roles allowing experienced staff to concentrate on customer interaction roles thus ensuring service quality and speed during the peak season. Because quality of service is consistent there is little time spent on correcting service quality so costs are reduced through a combination of less waste and better staff productivity. Overall flexibility enables achievement of performance objectives which increases return customer visits which keeps room occupancy high, thus spreading fixed costs and hence overall margins against sales revenue.
Central Evaluation Unit
Recently Veronique has recruited four new staff a change she believes will reduce the average throughput time for applications. Analyse the system using Littleâs Law and calculate what additional output per week can be forecast as a result of the staffing changes. Over a ten week period what impact would this extra capacity have on the number of applications in the system and how would this alter the days of throughput time? Please ensure that you show all the steps in your calculations with the objective of each step clearly stated. [50 Topic: Process design: Detailed process design,
Students are expected to use Littleâs Law to calculate the cycle time (0.188 hours or 11.3 minutes) so an output of 186 a week (1 / 0.188 x 35). Then the time to process one application is 0.188 x 28 staff so 5.27 hours per application. Staffing capacity has been increased by four. Working a 35 hour week this is an extra 140 hours which will process an additional 26.6 applications per week (140 / 5.27). Here better students will add this to the current output per week to give a new output of 213 a week (186 + 27). Alternatively, students can calculate the new cycle time (see below) and express this as the new output per week of 213. Over ten week this will reduce the number of applications in the system by (213-200) x 10 = 130. Currently there are 1340 so in ten weeks there will be 1210.
As we are now projecting the throughput time we need to calculate the new cycle time for the new staff levels. The new cycle time is 0.164 hours or 9.86 minutes (5.26 / 32); so throughput time is forecast to be around 31.4 days (0.164 x 1310 divided by 7 to give days) in ten weeks time. Depending on whether rounding is used (as above) and the assumptions made on the starting point of existing input of applications (the case is ambiguous on this) different answers will emerge all of which are acceptable as long as students show all the steps in their calculations with the objective of each step clearly articulated. See the Exam marking criteria matrix for levels of knowledge, communication and analysis. Central Evaluation Unit
Analyse the processing of application at the Central Evaluation Unit and calculate the number of hours it takes to process one application. What is the explanation for the long throughput time for applications? Evaluate how Veronique could improve throughput time. You are free to make assumptions to elaborate the case specifics but need to indicate that you are doing this. Please ensure that show all the steps in your calculations with the objective of each step clearly stated. [30] Topic: Process design: Detailed process design,
Students are expected to use Littleâs Law to calculate the cycle time (0.188 hours or 11.3 minutes) then the time to process one application is 0.188 x 28 staff so 5.27 hours per application. Alternatively students could work out the actual output per week (186.2) and divide this into the total hours worked per week (28 x35) to achieve the same answer. Students need to appreciate that the cause of the long throughput time is the high level of applications in process (1340) not the time take per application so ideas on improvement need to focus on reducing work in process levels. In the short term more capacity may be needed to do this. Reducing the amount of rework in the process will help as will introducing a better tracking systems so that time is not wasted physically finding applications etc. Littleâs law: Throughput Time = WIP x Cycle Time
Littleâs law: Throughput Time = WIP x Cycle Time
Throughput Time /WIP= Cycle Time
Throughput Time = 36 days
WIP = all in tray applications: 600+130+220+130+130+130 = 1340 (36 x 7*) /1340 = 0.188 hours = 11.3 minutes (0.188 x 60)) *number of hours in a day (35 / 5)
account these capacity restraints and defend the suitability of your ideas in achieving the profitable increase in visitor numbers. Your are free to make assumptions to expand the case material but ensure that you explain why you need to do this. [50] Topic: Capacity planning and control: What is capacity management? Measuring demand and capacity. Alternative capacity plans. See Slack pages 298-316.
Students need to appreciate that demand is seasonal and that peak demand each week is on Saturdays and Sundays. Calculations need to focus on the busiest months and for instance for August show the peak demand per day is 283 during 2007 (Aug 3400 /4 weeks /3) so 424 for 2008. Students should be able to identify from the case, with some simple calculations, that the current available capacity is constrained in the Milking Parlour to 80 per hour during a limited time frame of 2.5 hours so approx 200 is the maximum visitors per day for this attraction.. Car parking can cope with 240 coach visitors and car parking 160 visitors but car parking could easily be extended to field parking during dry periods. Topic Operations Management: Operations processes have different characteristics, The 4 Vâs Overview
All operations processes have one thing in common, they all take their âinputsâ like, raw materials, knowledge, capital, equipment and time and transform them into outputs (goods and services). They do this is different ways and the main four are known as the Four Vâs, Volume, Variety, Variation and Visibility.
To increase the number of farm visitors by 50% in a single year is a almost unachievable goal that Gillian has set for herself. Although it is possible that the number be increased, but going from 15000 visitors to 22500 visitors is not a small task which can be achieved in the duration of a single year. This is due to a number of factors which, for Gillian, would be constraints in achieving this growth target. These factors include: 1. The fact that the farm is open to visitors for 7 months in a year, during the remaining months the animals are kept inside and the rides etc available to customers are not safe due to the weather situation. This is a limit which Gillian would be unable to surmount in a single years time without capital investment into building sheds and indoor facilities etc at the Holly Farm.
Formula
Littleâs law: Throughput Time = WIP x Cycle Time
Throughput Time /WIP= Cycle Time
Throughput Time = 36 days
WIP = all in tray applications: 600+130+220+130+130+130 = 1340 (36 x 7*) /1340 = 0.188 hours = 11.3 minutes (0.188 x 60)) *number of hours in a day (35 / 5) Cycle time = ((y * h * 60) / z) Where y is throughput time, z is the work in process and h is the hours worked per week. (choose the process with the lowest effective capacity ) The efficiency of the factory = 100 * (p / y) Where p is the actual output and y is the lowest effective capacity of the bottleneck process (without PLP) To work out the planned losses you do (100-planned loss percentage)/100= And answer x design capacity e.g 1036x(100- planned loss percentage 22)/100= e.g 36/12 x 1.10 (rating) x 1.20 (+allowance)= 3.96
36 minutes, 12 cycle, rated effiecent 110%, allowance 20%
Desired cycle time in minutes = (d * w * 60) / z Where d in the number of days worked per week. w is the hours worked in a day and z is the output required per week. The product’s activities and the total minutes of work are not needed for this calculation.