Facility Layout
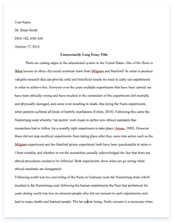
- Pages: 13
- Word count: 3073
- Category: Design Management
A limited time offer! Get a custom sample essay written according to your requirements urgent 3h delivery guaranteed
Order NowI.Introduction:
In this paper we will be discussing the facility layout. In which we will try to define it and know its objectives, factors that affect it and the different layout types. First we will start by trying to define and understand what facility layout is. Facilities are defined as the workspace and equipment needed to carry out the operations of the organization. This
includes offices, factories, computers, and trucks. The location, design, and layout of an organization’ facilities are central to maximizing the efficiency of the overall operations system.
Layout decisions entail determining the placement of departments, work groups within the departments, workstations, machines, and stock-holding points within a production facility. The objective is to arrange these elements in a way that ensures a smooth work flow (in a factory) or a particular traffic pattern (in a service organization). In general, the inputs to the layout decision are as follows:
1.Specification of the objectives and corresponding criteria to be used to evaluate the design. The amount of space required, and the distance that must be traveled between elements in the layout, are common basic criteria.
2.Estimates of product or service demand on the system.
3.Processing requirements in terms of number of operations and amount of flow between the elements in the layout. 4.Space requirements for the elements in the layout.
5.Space availability within the facility itself, or if this is a new facility, possible building configurations.
To conclude that we could say that, a facility layout is an arrangement of everything needed for production of goods or delivery of services. A facility is an entity that facilitates the performance of any job. It may be a machine tool, a work center, a manufacturing cell, a machine shop, a department, a warehouse, etc. (Heragu, 1997).
ii. Facility layout objectives:
Facility layout objectives can be summarized into 5 words “utilize-Eliminate- facilitate- Minimize – Provide”. As it utilizes space and labor, and eliminates bottle necks and waste/redundant movement, as for facilitation it Facilitate organization structure, communication and interaction between workers, manufacturing process, and visual control, it also minimize manufacturing cycle time or customer flow time and most of all the cash flow or the investment, last but not least is Providing convenience, safety and comfort of the employees along with flexibility to adapt to changing conditions.
iii. The Need for layout decision:
In this point we will be discussing some of the reasons that push us to take a layout decisions, such as; Changes in volume of output or mix of product; This aspect of facility design includes everything from making sure that traffic lanes are wide enough to making certain that inventory storage warehouses or rooms utilize as much vertical space as possible, and as J.K. Lasser said in How to run a small business, “While space does tend to fill itself up, receiving and shipping rarely get enough space for the work to be done effectively,” so that’s why we have to keep that in mind while making the layout. Ease of communication and support—Facilities should be laid out so that communication within various areas of the business and interactions with vendors and customers can be done in an easy and effective manner.
Similarly, support areas should be stationed in areas that help them to serve operating areas. Impact on employee morale and job satisfaction—since countless studies have indicated that employee morale has a major impact on productivity, Weiss and Gershon counsel owners and managers to heed this factor when pondering facility design alternatives: “Some ways layout design can increase morale are obvious, such as providing for light-colored walls, windows, space. Other ways are less obvious and not directly related to the production process. Some examples are including a cafeteria or even a gymnasium in the facility design.” Safety—The facility layout should enable the business to effectively operate in accordance with Occupational Safety and Health Administration guidelines and other legal restrictions. Changes in many aspects could lead to a layout decision such as change in the design of product or service, change in methods and equipment also change in environmental or other legal requirements. iiii. Factors affecting layout:
The final solution for a Layout has to take into account a balance among the characteristics and considerations of all factors affecting layout, in order to get the maximum advantages. The factors affecting layout can be grouped into 8 categories: 1.Materials:
The layout of the productive equipment will depend on the characteristics of the product to be managed at the facility, as well as the different parts and materials to work on. Main factors to be considered: size, shape, volume, weight, and the physical-chemical characteristics, since they influence the manufacturing methods and storage and material handling processes. The sequence and order of the operations will affect plant layout as well, taking into account the variety and quantity to produce. 2.Machinery:
Having information about the processes, machinery, tools and necessary equipment, as well as their use and requirements is essential to design a correct layout. Regarding machinery, we have to consider the type, total available for each type, as well as type and quantity of tools and equipment. It’s essential as well to know about space required, shape, height, weight, quantity and type of workers required, risks for the personnel, requirements of auxiliary services, etc. 3.Labor:
Labor has to be organized in the production process (direct labor, supervision and auxiliary services). In this point we have to put in mind two consideration first, Environment considerations: employees’ safety, light conditions, ventilation, temperature, noise, etc, Second; Process considerations: personnel qualifications, flexibility, number of workers required at a given time as well as the type of work to be performed by them. 4.Material Handling:
Minimize material handling as well as combining with other operations when possible, eliminating unnecessary and costly movements. As material handling does not add value to the product; it’s just waste. 5.Waiting time – Stock:
This factor should be put in mind in order to reach continuous Material Flow through the facility, avoiding the cost of waiting time and demurrages that happen when the flow stops On the other hand, the material waiting to flow through the facility not always represents a cost to avoid. As stock sometimes provides safety to protect production, improving customer service, allowing more economic batches, etc. It’s necessary then to consider space for the required stock at the facility when designing the layout. 6.Auxiliary Services:
The auxiliary services represent around 30% of the space at a facility. The space dedicated to auxiliary services is usually considered as waste. Its important to have efficient services to insure that their indirect costs have been minimized. Auxiliary services can be related to labor, material and machinery. 7.The building:
If it has been already selected, its characteristics will be a constraint at the moment of designing the layout, which is different if the building has to be built. 8.Future changes: One of the main objectives of plant layout is flexibility. It’s important to forecast the future changes to avoid having an inefficient plant layout in a short term. Flexibility can be reached keeping the original layout as free as possible regarding fixed characteristics, allowing the adjustment to emergencies and variations of the normal process activities. Possible future extensions of the facility must be taken into account, as well as the feasibility of production during re-layout.
V. Layout types:
The layout design generally depends on the products variety and the production volumes. Four types of organization are referred to, namely product layout , process layout, fixed product layout and cellular layout (Dilworth, 1996). First we will talk about product layout. This type of layout is useful when the production process is organized in a continuous or repetitive way. What its Continuous flow the correct operations flow is reached through the layout design and the equipment and machinery specifications. As for Repetitive flow (assembly line),The correct operations flow will be based in a line balancing exercise, in order to avoid problems generated by bottle necks. The layout will be based in allocating a machine as close as possible to the next one in line, in the correct sequence to manufacture the product. As everything this type has advantages and disadvantages, some of its advantages are;
1.Reducing material handling activities.
2.Working in Process almost eliminated.
3.Minimum manufacturing time.
4.Simplification of the production planning and control systems.
5.Tasks simplification.
As for the disadvantages:
1.No flexibility in the production process.
2.Low flexibility in the manufacturing times.
3.High capital investment.
4.Every workstation is critical to the process.
5.The lack of personnel or shut down of a machine stops the whole process.
6.Monotonous work.
Process layout is a bit different it’s a functional grouping of machines; this type of layout is useful when the production process is organized in batches. Personnel and equipment to perform the same function are allocated in the same area. The different items have to move from one area to another one, according to the sequence of operations previously established. The variety of products to produce will lead to a diversity of flows through the facility. The variations in the production volumes from one period to the next one (short periods of time) may lead to modifications in the manufactured quantities as well as the types of products to be produced. This type of layout is useful when the production process is organized in batches.
For example, a group of lathe machines are arranged in one area, drill machines in another area, grinding machines in another area and so on. Different job jumps from one area to another differently. Hence, the flow of jobs is difficult to perceive. This type of layout is suitable for a make-to-order or an assemble-to-order production environment, as in a job shop where customization is high, demand fluctuates, and volume of production low. Since a wide variety of products are produced, general purpose equipments and workers with varied skills are needed. Advantages of process layout are;
1.A process layout provides flexibility
2.Can handle a variety of processing requirements.
3.Equipment used is less costly
4.Possible to use individual incentive plans
Disadvantages of process layout:
1.In-Process inventory could be high.
2.Challenging routing and scheduling
3.Equipment utilization rates are low.
Now we will go through the fixed position layout, it’s a production technique used to assemble products that are too large, bulky, or fragile to safety or effectively move to a location for completion. In a fixed position layout, personnel, supplies, and equipment are brought to the site where the product will be assembled, rather than the product being moved through an assembly line or set of assembly stations. Advantages of fixed position are;
1.Material movement is reduced.
2.Provides job enrichment opportunities.
3.Promotes pride and quality because an individual can complete the whole job.
4.Highly flexible; can accommodate changes in product design , product mix and product volume. Some of the disadvantages are;
1.Personal and equipment movement is increased.
2.May result in duplicate equipment.
3.Requires greater skill for personal.
4.Requires general supervision.
5.May result in increased space and greater work-in process.
6.Requires close control and coordination in scheduling production.
The last type we are going to discuss is the Cellular layout type it’s the newest type introduced. Cellular manufacturing is a type of layout where machines are grouped according to the process requirements for a set of similar items (part families) that require similar processing. These groups are called cells. Therefore, a cellular layout is an equipment layout configured to support cellular manufacturing. Processes are grouped into cells using a technique known as group technology (GT). Group technology involves identifying parts with similar design characteristics (size, shape, and function) and similar process characteristics (type of processing required, available machinery that performs this type of process, and processing sequence).
Workers in cellular layouts are cross-trained so that they can operate all the equipment within the cell and take responsibility for its output. Sometimes the cells feed into an assembly line that produces the final product. In some cases a cell is formed by dedicating certain equipment to the production of a family of parts without actually moving the equipment into a physical cell (these are called virtual or nominal cells). In this way, the firm avoids the burden of rearranging its current layout. However, physical cells are more common. An automated version of cellular manufacturing is the flexible manufacturing system (FMS). With an FMS, a computer controls the transfer of parts to the various processes, enabling manufacturers to achieve some of the benefits of product layouts while maintaining the flexibility of small batch production. Some of the advantages of cellular layout are;
1.Reduced material handling and transit time.
2.Reduced setup time.
3.Reduced work-in-process inventory.
4.Better use of human resources:
a.Self-managed team, in most cases more satisfied with the work that they do b.Flexible resource. Workers in each cell are multifunctional and can be assigned to different routes within a cell or between cells as demand volume changes.
5.Easier to control.
6.Easier to automate.
As for the disadvantages they could be summarized in;
1.Inadequate part families
Part families identified for design purposes may not be appropriate for manufacturing purposes.
2.Poorly balanced cells
It is more difficult to balance the flow of work through a cell than a single-product assembly line, because items may follow different sequences through the cell that require different machines or processing times.
3.Expanded training and scheduling of workers
Training workers to do different tasks is expensive and time-consuming and requires the workers’ consent. 4.Increased capital investment
a.Existing equipment may be too large to fit into cells or may be underutilized when placed in a single cell. b.Additional machines of the same type may have to be purchased for different cells. c.The cost and downtime required to move machines can also be high.
VI. Conclusion:
Facility layout must be considered very carefully because we do not want to constantly redesign the facility. Some of the goals in designing the facility are to ensure a minimum amount of materials handling, to avoid bottlenecks, to minimize machine interference, to ensure high employee morale and safety, and to ensure flexibility. Facility managers should consider several factors when designing the layout of a facility to achieve maximum effectiveness, such as; •Does the design and layout allow for growth or change? Is there a chance that your company will experience significant growth? Could some other change come about that could influence the layout of your facility? In business, anything is possible.
Make sure that same is true of your facilities layout. While making changes is a costly and undertaking them shouldn’t be taken lightly, your layout should be flexible enough to allow a redesign if the situation calls for it. •Is the process flow smooth? If you are running a factory, for example, the flow should be such that the raw materials enter at one end and the finished product exits at the other. The flow doesn’t have to form a straight line, but there should be no backtracking. Backtracking creates confusion. Employees get confused (“Has that been done yet? “), parts get lost, and coordination is very difficult.
You need to have a smooth process to be efficient. •Are materials being handled efficiently? Here simplicity is best. •Does the facility layout aid the business in meeting its production needs? Is there enough space and is it used efficiently? Have you allowed enough space for shipping and receiving? Can different areas of the business communicate effectively? Does the layout lend itself to promotional activities? (e.g., showing the facilities to potential customers) •Does the layout contribute to employee satisfaction and moral? Numerous studies have linked employee moral to productivity. So managers should take this point into consideration when designing the layout of their facilities. How can this be done? Paint the walls light colors, allow for windows and space, and include a cafeteria and a gym. Some of the options may cost lots of money, but if it increases productivity in the long run, it is probably worth making the investment.
VII. Applying on case:
To apply what we have discussed I choose Payless shops, Payless ShoeSource is dedicated to democratizing on-trend and validated styles in footwear and accessories for the world. Payless is a specialty family shoe store serving women, kids, teens and men for their everyday needs and fashion wants at incredible value and quality. In the mean while Payless has already 10 branches in cairo. The reason why I chose Payless is because of the very unique layout of the shop. They have introduced a new style of layout in the shoesource field. When you get inside the shop you will find the layout similar to a hyper market layout where there is rows and shelves.
Above each row you will find a sign with the shoe size the shelves in this row have. And above each shelve is the stock. They don’t put the stock inside the storage room. This layout makes it easy for you to find what you’re looking for, as you go directly to your shoe size row and search for the model and color you want, instead of wasting time choosing model and color and then asking the sales person for your size and then finding out they don’t have it. Those pictures of how the shop and shelves look like.
Whats more amazing is the way the kids shoe shelves, they start by putting the girls shoes in the lower shelves then they boys and this is because girls love to shop from an early age and they like to choose what they want to wear themselves but boys as usual hate shopping so their mums and dads are the ones who shop and chooses for them. Below is a picture to illustrate. At Payless to make a decision about layout planning, 4 different questions must have an answer:
1.Which centers do we have to consider?
2.How much space and capacity is required for each center?
•Too much space is expensive and may also reduce productivity.
3.How must the space be configured at each center?
•Space quantity, shape and the elements of the work center are related to each other.
4.Where should each center be located at within the facility?
•The allocation of the different centers may affect productivity.
After answering those questions layout decision is easy and quickly taken. From my point of view what gives Payless the edge over competitors beside the price is the layout, as it makes the shopping experience very easy, quick and progressive.
VIII. References:
1.http://www.inc.com/encyclopedia/facility-layout-and-design.html 2.http://home.snc.edu/eliotelfner/333/bricks/Layout.html
3.https://www.boundless.com/business/operations-management/planning-for-operations/facilities-layout/ 4.http://www.ateneonline.it/chase2e/studenti/tn/6184-7_tn05.pdf 5.http://www.referenceforbusiness.com/management/Int-Loc/Layout.html#ixzz30PLJqLX6 6.http://www.mdcegypt.com/Pages/Operation%20Management/Production%20&%20Operation%20Management/Facility%20Layout/Facility%20Layout%20Cellular%20Layouts/Facility%20Layout%20Cellular%20Layouts.asp 7.http://www.referenceforbusiness.com/management/Int-Loc/Layout.html#ixzz30PLJqLX6