The Realco Breadmaster
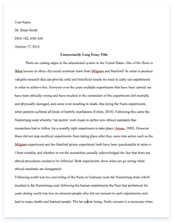
- Pages: 10
- Word count: 2495
- Category: Customer
A limited time offer! Get a custom sample essay written according to your requirements urgent 3h delivery guaranteed
Order NowA master production schedule (MPS) is a plan for individual commodities to produce in each time period such as production, staffing, inventory, etc. The process of developing a master production schedule includes calculating the projected on-hand inventory and determining the timing and size of the production quantities of specific products. There are many advantages to developing a MPS within a company. With the case study of The Realco Breadmaster in chapter 15, we will develop a master production schedule and answer the other questions that are related to the case study. This diagram allows us to have a simplified understanding of the results and benefits of what information and aspects of the company a master production schedule will take into consideration and what the resulting information to gain will be. We cans see from the diagram below that end result of a well=organized MPS can benefit Realco by giving them the amounts to be produced, the correct staffing levels needed, the available inventory to promise, and their projected available balance. It allows Realco as a company to simply be on the same page.
Realco has not overpromised, but instead it is clear that the bread-makers produced are far much greater than the demand anticipated. Therefore, Realco is going to be left with an excess of inventory if they continue the route that has been established up front. The master production schedule that I have come up with will allow them not to have as much excess inventory, even though Realco could adjust the production numbers to 25,000 due to Jack Jones having the highest order at 23,500.
There are advantages and disadvantages to the way Jack Jones is promising orders. The main advantages to the way Jack is promising orders is that there won’t be an order that would go unfilled, and he could promise them to have the orders out on time. Yet, the major disadvantage is that at the end of year mark he will be left with a major overflow of bread-makers, therefore it is very important to have a schedule to guide in the process. Scheduling is an important tool for manufacturing, where it can have a major impact on the productivity of a process. In manufacturing, the purpose of scheduling is to minimize the production time and costs, by telling a production facility when to make, with which staff, and on which equipment. Production scheduling aims to maximize the efficiency of the operation and reduce costs
There are a five main ways formal master scheduling would improve this process overall for Jack Jones and his bread-masters. First, it can help to smooth the demand signal, because most customer demand signals will contain peaks and troughs of demand. Second, it protects lead time and helps book future deliveries. Also, a formal master production schedule acts as a single communication tool to the business. The fourth idea is that it would improve the overall process in that is helps the supply chain prioritize requirement, and this allows for the supply chain team to be more effective. Lastly, it just overall helps to stabilize production to the point the right amount of product is being produced.
To determine whether or not it is more detrimental to a company to refuse a customer’s order upfront because you don’t have the units available or accepting the order and then failing to deliver, we have to take a look at it from the customers perspective. If I, as a customer, order a product or service from a company and they promise that it will be done, yet it is not delivered I would be pretty upset with that company for promising and not delivering. Now, if that same company told me up front that they could not provide me service at the time due to some type of circumstance, I would be more apt to do business with them at a later time in these circumstances. From here, we can see that for Jack Jones to have a more precise inventory control instead of an overflow or shortage it would be more profitable. This is the idea behind the master production schedule, which allows everyone to be on the same page and time frame with the amount of product that is going to be produced in a certain period of time. “The Master Production Schedule (MPS) is essential in maintaining customer service levels and stabilizing production planning in a Material Requirements Planning environment.” (Tang, 323) Realco would be able to be more satisfactory for their customer’s sake.
If Realco decided on a master production schedule that allowed them to produce 20,000 breadmakers every week instead of 40,000 every week, it would have a huge impact on the business altogether. Since, Realco over projected in the beginning with the amount of breadmakers they needed to produce each week, even though they were going to be able to cover the necessary demands, they would be left with a great overstock after the 8 week schedule that was put together. All companies are in the business to save money, therefore anyway that Realco could save money, it would mean for a greater profit and more revenue for them. Therefore, if Realco decided to decrease their master production schedule from 40,000 to 20,000 then they would save money on material and the production side of things. Now if the Realco does this, they have to understand that they may not be able to fill every one of their orders on the time schedule that they had originally promised. It may take an extra week or two for them to cover the 23,500 order from week one. But they will be able to fill it in time, and this is better than setting the customer’s expectation that the order will be able to be filled and not delivering. This also allows for the company to be on the same page of expectation for production for the customer’s benefit, while saving money.
With the case study of The Realco Breadmaster in chapter 15, we developed a master production schedule and answer the other questions that are related to the case study. We saw how the master production scheduling can change the process of procedures within a company for the benefit of the customers and company’s revenue in mind. A master production schedule is a must for any company that wants to succeed and achieve within their industry.
A Bumpy Road for Toyota
Toyota was able to greatly reduce lead time and cost using the TPS, while improving quality. This allowed Toyota to become one of the ten largest companies in the world. It is currently as profitable as all the other car companies combined and became the largest car manufacturer in 2007. Toyota will continue to grow its company, but can you exchange growth for quality? “To stop the quality slide, Mr. Cho, [Toyota’s President] says Toyota has launched multiple “special task forces” at trouble spots in places such as North America and China to overhaul shop-floor management.” (Bozarth, 548) From chapter 16 case study A Bumpy Road for Toyota, we will discuss the four questions that deal with the Lean philosophy, who the coordinators were in Toyota’s production system, what went wrong with Detroit’s approach to Lean, and what Toyota is doing about “Haste makes Waste” idea. “The use of the term ‘Lean,’ in a business or manufacturing environment, describes a philosophy that incorporates a collection of tools and techniques into the business processes to optimize time, human resources, assets, and productivity, while improving the quality level of products and services to their customers.
Becoming ‘Lean’ is a commitment to a process and a tremendous learning experience should you attempt to implement Lean principles and practices into your organization.” (Becker, 1) Is Toyota’s focus on quality consistent with the Lean philosophy? By looking at the case study, we can see that Mr. Cho, Toyota’s president, says, “Quality isn’t improving as fast as it should” and Gary Convis says, “We are getting back to the basics.” The idea of the Lean philosophy that I believe Toyota is missing is the focus on and benefit of customer. If a company focuses just on only what they can gain like assets or production amount, they can negate the whole reason for the production and success, customers. If a company doesn’t have customer satisfaction, they will more than likely not have customers. At the end of the day, the amount of customers and satisfaction of customers depends on whether the company expands or detracts. Toyota seemed to have merely de-toured from foundational route that lead them to the original success, especially within the Georgetown, KY branch. Can a firm actually follow the Lean philosophy and not have a strong quality focus? No, because what a firm implements the Lean philosophy into their firm for is to grow the firm’s assets and production level, while maintaining quality.
If a firm negates quality, they might as well give more than half of their customer base and incentive to go to the competitor. If you remove quality you might as well remove the philosophy altogether. The coordinators that the case study talks about are not the top executives, but 1980s midlevel Japanese managers who helped to control the great expansion of Toyota to the United States. “These coordinators were experts in Toyota’s Lean-manufacturing techniques and philosophies, commonly known as the Toyota Production System, or TPS.” (Bozarth, 548) The coordinators, or Japanese managers, were experts in the Toyota Production System techniques and philosophies. These coordinators were took the hands on approach to teach the American shop-floor managers and hourly associates by attacking the issues directly on the assembly line. They did take hours upon hours of learning out of books in a classroom but literally taught hands on, which allowed for a faster and more profitable learning environment for the company and its employees. These coordinators are going to be hard to replicate because of their personal 20-years or more experience within the industry. The longevity of these coordinators cannot be found in each and every company on a day to day basis. Toyota was lucky to have found such committed and loyal employees for this dramatic transition into the U.S.
Hajime Oba, a retired TPS guru, was used for case to case basis within Toyota to better the company’s performance through the TPS process. Oba says, “They are creating a Buddha image and forgetting to inject soul into [the process]” (Bozarth, 548) What he means by this is that the structure is there to go by, but the employee’s need to take more of a care and desire to perform and do good by the customers and for the customers. Overall, if Detroit would focus a little more on the “why” instead of the “what” they are doing, there would be more profitable and beneficial results. I would have to say that I do agree with Mr. Oba’s philosophy, because the major problem that is follows manufacturers within the U.S. is that the firms want to produce more and more and not worry as much about quality. Where Porsche and Lexus are taking more time on each car and producing quality with higher prices, they continue to top the charts every year.
The biggest issue within the Georgetown branch for Toyota, Mr. Oba says, is that the shop-floor managers are spending too much time within the offices and not enough time on the floor coaching and teaching the other employees. If we look back at the original formation of the Georgetown branch we saw that the original coordinators took the time to coach and teach the employees within each step by telling them through the experience that they had the most beneficial way of conducting their job. This allowed for a quicker process of learning and better implementation of procedures. The firm could be run as it supposed to with the managers fixing issues as they occurred because they were there watching what was going on. I am sure this gave the employees more of a care for their job because of the care those coordinators took for them to learn.
Therefore, overall they saw a satisfaction from the employee for the help and aid they were receiving, and the managers-coordinators could rest easy at night knowing that their jobs were secure and done properly. In an industry like that, because of the managers care, it would be seen and overflow to the customers, who are the main element in the equation. Through the years, the Georgetown branch forgot this and left a major part of the Lean philosophy behind. They were pursuing the “Haste makes Waste” way of production, and this can look good up front but have a bitter bite of loss on the back end. To shake things up, Mr. Oba and Mr. Convis drug about 70 midlevel managers through their employee’s shoes to embarrass them and show them the need to learn more about the Toyota Production System. This has formed into a more Organization Development Group, and continues to this day to get those Georgetown and Detroit firms back to the standard they were originally run at by the 20-year experienced coordinators.
Although, they will most likely not achieve the amount of success for quality and assurance of the Lean production level they once held, this is Toyota’s push to pursue that goal. From chapter 16 case study A Bumpy Road for Toyota, we have discussed the four questions that deal with the Lean philosophy, who the coordinators were in Toyota’s production system, what went wrong with Detroit’s approach to Lean, and what Toyota is doing about “Haste makes Waste” idea. We have seen that Toyota is pushing to regain control of the level within the approach to Lean that they once help to top the two controllers of the scoreboard, Porsche and Lexus. “Implementation requires a commitment and support by management, and participation of the all personnel within an organization to be successful”, says the creator of TPS, Taiichi Ohno. (Ohno, 1) With this understand, Toyota will regain the once held customer satisfaction they once had.
References
Becker, Ronald M. (2013) SAE International. The People and Ideas That Have Shaped Modern
Business by Daniel A. Wren and Ronald G. Greenwood. Oxford University Press – New
York 1998.
Bozarth, C.C. and Handfield, R.B. (2008). Introduction to operations and supply chain management (2nd ed.). Upper Saddle River, New Jersey: Pearson Prentice Hall. ISBN: 9780558317867
Hugos, Michael H. What are the key benefits of Master Production Scheduling? http://supplychain-mechanic.com/?p=204
Ohno, Taiichi (2013) SAE International. The People and Ideas That Have Shaped Modern
Business by Daniel A. Wren and Ronald G. Greenwood. Oxford University Press – New
York 1998.
Tang, O., & Robert, W. G. (2002). Planning and replanning the master production schedule under demand uncertainty. International Journal of
Production Economics, 78(3), 323-334. Retrieved from http://search.proquest.com/docview/198951274?accountid=32521