Taguchi Loss Function
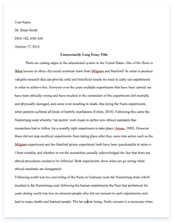
- Pages: 10
- Word count: 2442
- Category: Customer
A limited time offer! Get a custom sample essay written according to your requirements urgent 3h delivery guaranteed
Order NowThe term Taguchi methods usually cover, two broad based ideas. The first idea deals with use of statistical methods that concerns itself with analysis of variance. In order to enable an elaborate identification of the principle design factors responsible for degrading product performance, the model user may construct experiments to aid understanding. The other concept argues that when dealing with judgment of effectiveness of designs, the extent of loss is a function of the “deviation of any design parameter from its target value” (El Sayed, M. & Hsaing, C. G., Taguchi, 1989).
The focus of Taguchi’s approach to design is that of measuring quality, and the method normally referred to as loss function measuring quality. The loss function is a method that establishes in a business organization, a financial measure of the user dissatisfaction with a product’s performance as it deviates from the set target value, (Quality Management & Training Limited 2002). As such performances that are considered average together with variation are core factors central to measure of quality. In his argument, selecting the design for a product or a manufacturing process that is deemed insensitive to uncontrolled variation sources help in the improvement on quality of that particular product. These factors that are uncontrolled sources of variations are timed by Taguchi as noise factors. This idea that led to use of this term was born out of early applications of his methods that were carried out in the communications industry.
Inorder for one to apply this concept it is proper that you evaluate (in your work) the variance, and the mean (average) for the technical bench marking in Quality Function Development (QFD). Thus, the loss function would present you with the opportunity of a single metric for comparison. Quality Function Development refers to a detailed approach that defines the requirements and transforming them into specific strategic plans to process products that meet these requirements, (Alejandro S, 2003).
The Taguchi methods are not merely a statistical application based on design of experiments alone but, also inclusive of integration of the statistical design into a broader and more powerful engineering process. The true power behind this application is in its simplicity to be implemented.
These static applications as envisaged by Taguchi, look for a design of a product or process that achieves a single (one) fixed level of performance. According to him for a single mold designs the best operating conditions lie in the static application for an injection-molding machine. Generally mold dimensions are used in dynamic applications as the basic signed and search to operating conditions that would generate a similar or even equivalent percent shrink for any orientation in any given single dimension.
In its approach, Taguchi explains that the dynamic applications offers an organization the opportunity to produce a design that is satisfactory in its requirement with respect to the modern day demands, but at the same time it has the flexibility of being molded to fit within context of tomorrow or for future demand. This latter approach can a matter of fact be considered as a contingency planning strategy for the yet to be discovered future needs (http://curiouscat.com/management/lossfunction.cfm. Within its application (dynamic) a signal factor shifts the performance to a new value and a factor known as an adjustment factor helps to modify the particular designs sensitivity to fit within the description of this factor.
In order to understand the basis of this methodology and have a wider understanding of the whole application, Taguchi proposes that you plot a straight line relationship with the signal factor on the X-axis and the response on the Y-axis. The adjustment factor will however, be the determinant as to the changes that occur to the slope (gradient) of the line. It is also very much in order and useful to be able to reduce the sensitivity of a product to match with the changes in the signal. For instance, when a manufacturer is designing a sports car, his/her desired finished product might be that the car that provides the driver with an opportunity to have a feel of the road. In this case the signal factor would be the controlling knob setting of the car. Further analysis of this scenario may reveal that the adjustment factor would actually be the suspension system.
The adjustment factor would help determine the extent and magnitude of change in the setting of the knob. Other various design specifications would attest to a predictable link between the knob setting and that of road feel. Other variables in this case, such as the variations in the conditions of the weather and road in essence would have negligible effect upon this relationship between the knob adjustment and the feeling the driver gets from the road.
In another scenario, the voice of the customer to a greater extent aids organizations in creating good systems designs. Most organizational units use focus groups marshal input for their designs. For example, according to Martin Justin, (1995), ignore your customer, Fortune magazine, several examples of products voices were not purchased by consumers. According to him, if consumers were studied under more natural conditions then additional information that would be very useful would be obtained.
As another terminology that has been advocated for since 1985, known as Gemba would be a crucial step toward QFD. Gemba can generally be termed as the total environment (surrounding) under which a consumer lives and works.
The three compounds constituting voice of the consumer table would be; the verbatim response from customer, the context of use and integration of the customer’s verbatim response and its context. Finally the organizational unit would thus, divides the expanded list of customers information into; failure modes, demanded qualities by consumers, solutions among others. The context of application would therefore help to identify some of the environmental sources of uncontrolled variation in the performance of processing for the particular products. For example, sources of variation that concerns an Easel pad include; the force applied to the paper, humidity and if it is being used within or outside. As such the Taguchi¢s Robust Design reduces its effect caused by the uncontrolled sources of variations to the performance of the product.
HOW TO MEASURE QUALITY
As shown in the figure 1 below, quality has traditionally been viewed as a stop function as indicated by the thick line graph in the figure. In essence a product is either good or bad and has no intermediate position. The assumption that this view hold is that a product is uniformly good between the specifications of upper specifications (US) and lower specification (LS). The vertical axis represents the US (lower specifications) which is virtually the extent to which customers and displeased with the performance of the product. Curves A and B represent the frequencies of performance level of two particular designs over a certain period of time. Accounting for the graph, B can be said to have a higher fraction bad performance level and as such is less desirable as compared to A by the customers.
In certain instances both the Taguchi loss function use and the traditional decision makers would arrive at similar decisions. This would be as a result in the organizations considering that the mean, position, and variable as well as the means are equal and/ or the variances too being equal. The only variation would be chart of calculating percent defective as the traditional decision would be calculating if over time while both mean and variance are different.
According to Taguchi, the dissatisfaction level of a consumer is directly proportional to the deviations from target by performance of a product i.e. the consumer increasingly becomes dissatisfied as the level of performance of a product deviates further from the targets it set to meet. As such he suggests that a quadratic curve representing the level of dissatisfaction of a customer with products¢ performance be used.
The first dedicative becomes the quadratic curve when the Taylor¢s service expansion about the target of performance is set at zero. The centrality of the curve becomes the target value, which in essence gives the best performance level in the consumer’s opinion. However, it is not a very easy task to identify the best value. In some cases the designer¢s best guess usually become the targets.
According to the graph above LCT, stands for the lower consumer tolerance while UCT represents the upper consumer tolerance. In this view the design is customer driven rather than the more engineer¢s specification. Expert opinion in most cases refers to consumer tolerance to be the performance level, where 50% of the consumers are dissatisfied with the product. In other words a particular organizations specific circumstance would shape the definition of consumer tolerance for a product to its employees.
The equation for the mean loss is usually given as BELOW
This equation for the target is best loss function takes into account the mean and variance in the selection of the best design. In the calculations of the mean loss allows the design unit to take into account the benefit of cost analysis of other optional designs that have different costs yielding different men losses. As exhibited in the second figure, there is likely to be financial loss at the UCT. This is effect would present the organization with a warranty chance that might lead to repair loss.
In most applications involving loss function in QFD the value of K can be set at 1 as the constant would remain the same value for all competitors in relation to consumer. The account of the graphs portrays a symmetric loss about target that however, may not always be the case. For instance, if products A and B have the same variance but unequal means, then the product with its average closer to the target (A) is viewed to have a better quality.
As illustrated in figure 4, if there are two products with the same mean but different variance, then the product with the smaller variance is viewed to have a better quality. The product B unlike its competitor seldom performs near target.
When calculating average loss for cases with different means and variances, the assumption is made that the one is in agreement with concept of loss function. In this case the product that has a smaller loss is viewed to have a better quality, like in figure 5.
LOSS FUNCTIONS AND TECHNICAL BENCH MARKING
In a real environment it is advisable for organizational teams to collect data obtained for technical bench marking. The definition of a real environment is that where everything remains uncontrolled and ideal. As such our product would be evaluated at varying temperatures, humidity and other climatic conditions to that of our competitors. It is possible to simulate these conditions in a laboratory. This is possible by varying environmental conditions in assessing the performance level of a product, as you would need to obtain realistic data so as to calculate the real world variance, (R. Sreenivas Rao et al 2004)
To define a well-balanced study of varying environmental conditions, it is proper to have an orthogonal array. A good estimate of the changing environmental conditions would be provided for by the 2 or 3 basic environmental conditions, each at 2 levels.
The orthogonal approach employs a special subset of the light combinations. As such the effect brought about by the missing four can be predicted due to the balanced nature of if combinations
Variance and loss calculations can be fractured into two extra rows at the bottom of the demand quality against performance level matrix as used in QFD. In this case the proportional ratio of average of loss of competitor A to that of B is independent of K (constant). The mean, variance and even loss ratio information is thus used to identify the directions for improvement as is specified for under the definition of average loss equation (http://www.mftrou.com/genichi-taguchi.html).
CONCLUSION
Dr. Taguchi’s contribution to engineering and statistics has been a valuable piece of methodology. The techniques, he employ in loss function to analyze variation in experiments, the general view of his strategy for system analysis, parameter as well as tolerance design are the hallmark of his general influence to improving quality of manufacturing processes globally. His considerations are based on the consideration for quality loss down to the customer level (Lyndsay S, 2007)
His methodology lays a lot of emphasis on “quality through robust design” rather than through inspection. He simplifies the design process into three steps
- System design – entails the creation of a working pro-type
- Parameter design – this entails the process of finding what factors are influential in the level of product performance through experiments
- Tolerance designs – this is based on the theory of setting tolerance limits at tight levels for the critical factors and a looser tolerance limit level for the less significant factors, (Nair, V N, 1992)
The robust design methodologies let the designs to determine through trials, the factors that would influence performance level of product and also to determine the insignificant factors. Thus the designer has the opportunity to minimize the variations within the critical factors. Thus, the “noise” factors can then be ignored, as their contribution to performance level of a product is negligible. With these methodologies it is possible to set up experiments that would investigate various combination factors with a statistical analysis of both mean and variance you are able to understand the most significant factors for your process. As such this knowledge would be valuable in a designing a process that enables and ensures consistency in good performance level.
Reference:
Alejandro Soto, (2003), Quality Function Development. SigmaSix
El Sayed, M. & Hsaing, C, Taguchi, G, (1989). Quality engineering and production
systems. New York: McGraw-Hill.
Lindsay Swinton, sigmasix Availabe at:
http://www.sixsigmaspc.com/dictionary/loss-function.html as retrieved on 15 Sep
2007 04:18:34 GMT.
Matt Seaver, (20003), Handbook for Quality Management, 3rd Ed. Gower publishing
Martin Justin, (April 1995), ignore your customer, fortune magazine,
Moen, R D; Nolan, T W & Provost, L P (1991) Improving Quality Through Planned
Experimentation
Mohamed Zairi, (1993), Total Quality Management for Engineers. Gulf publishing
- Sreenivas Rao, R.S. Prakasham, K. Krishna Prasad, S. Rajesham,P.N. Sarma, L.
Venkateswar Rao (2004) Xylitol production by Candida sp.: parameter
optimization using Taguchi approach, Process Biochemistry 39:951-956
http://www.dnh.mv.net/ipusers/rm/index.html