Purchasing: Hybrid Organizational Structure
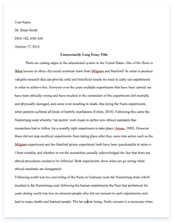
- Pages: 12
- Word count: 2980
- Category: Organizational Behavior Organizational Structure Structures
A limited time offer! Get a custom sample essay written according to your requirements urgent 3h delivery guaranteed
Order NowPurchasing and supply management as part of business management Purchasing and Supply planning is part of the firms general planning mainly because the continuous supply of raw materials, materials , components and services is of strategic importance to the enterprise. The Organizational structure of the purchasing and supply function should be aimed mainly at linking into the firms overall structure in the most effective way. Purchasing and supply coordination should be aimed at harmonizing and aligning the activities of the purchasing and supply function with those of the other business functions. Control is that element of management which ensures that the activities are executed according to plan and within the allowed parameters. NB. Purchasing and supply planning is the first responsibility of purchasing and supply management. The other management tasks (organization, coordination and control) can only be executed after the planning task has been completed.
Levels of Purchasing and supply planning and objectives:
3 levels:
Highest level – Organizational planning (strategic planning) Middle management Level – Functional and Tactical Planning Lowest Level – Operational Planning at the Lowest Level.
All interlinked and all should support each level.
Highest level – Organizational planning (strategic planning) Overall planning of the enterprise – Long term or strategic planning *Ensure purchasing requirements at competitive pricing
*develop existing or new suppliers
* keep investment in inventory as low as possible
Middle management Level – Functional and Tactical Planning Objectives:
*To enter into long term contracts with reliable suppliers of materials *To put together a project team responsible for developing suppliers *To study alternative inventory control systems or the flow of materials to and within the enterprise. Purchasing ahs supply planning at middle management level entails formulating derived objectives, planning and effective application if resources. Categories:
1. Needs
Enterprises needs for raw materials, materials, parts and services over the medium term must be determined. – Depends to a large degree on marketing research, marketing and sales estimates and the master production schedule for a reliable estimate of the quantity and variety of materials likely to be required by the firm. 2.Purchasing and supply program planning
Keyword: “external” Transport, deliveries , quantities required, contracts Development of plans and programmes to provide for estimated needs in the most efficient way, Planning for time scheduled deliveries, planning of transport, preparing the materials budget for the quantities required, preparing and negotiating contracts and agreements with suppliers. Important for planning: JIT, MRP
3.Purchasing and supply system
Keyword: Inventory, system planning, training, information system Planning category includes determining procedures for purchasing activities, planning inventory investment and inventory control system, planning for personnel training and development , as well as planning the information system. Important for planning EDI,MRPII
4.Extraordinary Project
Planning for extraordinary projects – Planning at middle management level for purchasing and supply function – Purchasing capital equipment, change to the organizational structure of the purchasing and supply function and planning by large contracts between 2-5yrs.
Lowest Level – Operational Planning at the Lowest Level. *To maintain sound relations with suppliers by means of ethical conduct and adherence to contract clauses, and also to order on time. *To study the situation in the supplier market and provide technical support to developing suppliers. *To conduct an inventory analysis, reduce A category products improve the understanding with suppliers or implement JIT. Planning for specific purchasing and supply activities over short term. 1. Materials requirement planning (MRP)
A materials requirement planning (MRP) information system is a sales forecast-based system used to schedule raw material deliveries and quantities, given assumptions of machine and labor units required to fulfill a sales forecast.
2. Supply Planning
Involves Negotiation, calculating the most economic order quantities and choosing supplier sources.
3. Planning the purchasing and supply system
Planning of the purchasing and supply system means that specific supply activities are allocated to subgroups in the purchasing and supply function and that a purchasing and supply manual is compiled , setting out the procedures for purchasing and supply activities.
Keywords: Manual and procedures
4. Extraordinary Projects
It is important to emphasize that in these cases, too operational planning deals with specific activities that should be achieved in the short term, for example what the enterprise wishes to achieve in negotiating a particular purchasing transaction. Purchasing and supply planning is therefore integrated to an important degree in all three hierarchical levels.
ORGANISATION OF PURCHASING AND SUPPLY MANAGEMENT
The creation of an effective organizational structure for the purchasing and supply function is a threefold process. 1. Firstly a decision is made about the position of the purchasing and supply function in the broad organizational structure of the enterprise. 2. The internal organizational structure of the purchasing and supply function is formulated, 3. Management decides on the extent to which all activities relating to the supply of materials should be integrated with other functions in the organization and with supplier networks – according to the supply chain management approach and eventually the virtual enterprise.
POSITION OF PURCHASING AND SUPPLY FUNCTION IN ENTERPRISE’S ORGANISATIONAL STRUCTURE
READ TEXT
* Organization of the purchasing function is affected by factors such as the following: The extent of the monetary value
ď€Şď€ the perceptual contribution of purchasing and supply to the enterprise’s profit ď€Şď€ the possibility of increasing profit
the variety and nature of materials to be purchased
ď€Şď€ the type of supplier market
ď€Şď€ time-based competition
ď€Şď€ the size of the enterprise
ď€Şď€ management’s commitment to integration
Centralization versus Decentralization
It is suggested that organizations centralize purchasing when purchases are a very high percentage of product cost or budget; items used by most of the operating units; or management feels the need for tight control over purchases. There are many advantages and disadvantages to centralize/decentralize. Your book on pages 78 through 86 lists many of them: ď‚· Coordinate Purchase Volumes
ď‚· Reduced Duplication of Purchasing Effort
ď‚· Ability to Develop and Coordinate Procurement Strategy
ď‚· Ability to Coordinate and Manage Company wide Purchasing Systems ď‚· Development of Purchasing Expertise
ď‚· Managing Change to Benefit the Entire Organization.
I would add to the list of advantages of centralization::
ď‚· Haphazard purchasing practices are minimized.
ď‚· Inventory control enhanced.
 Reduces work of others who don’t have that responsibility.  Fewer orders, less operating expenses.
ď‚· Communication with suppliers enhanced through consolidation. ď‚· It is easier to standardize the items brought if purchasing decisions go through one central control point. ď‚· By combining requirements, “clout” is generated by discussing an order quantity that is large enough to really get the supplier’s interest and reduced freight costs by reducing deliveries. ď‚· In period of materials shortages, one department does not compete with another department. ď‚· It is administratively more efficient for suppliers since they need not call on several people within the company. ď‚· It provides better control over purchase commitments thereby reducing the possibility of illegal or unethical practices. As one would imagine, there are disadvantages to centralization set out in an article from Purchasing Today:: * Narrow specialization and job boredom
* Lack of job flexibility
* Corporate staff appears excessive
* Tendency to minimize legitimate differences in requirements * Lack of recognition of unique needs
* Focus of corporate requirements, not on business unit strategic requirements * Most knowledge sharing one-way
* Common suppliers behave differently in geographic and market segments * Distance from users
* Tendency to create organizational silos
* Customer segments require adaptability to unique situations * Top management not able to spend time on suppliers
* Lack of business unit focus
* High visibility of purchasing costs
However, there are times when it makes sense to decentralize. You frequently see decentralized purchasing when companies process single natural raw materials; technically oriented firms that are heavily involved in research (scientists); operation of multi-site institutional & manufacturing organizations (centralized planning at corporate level, ordering at plant level); autonomy of a manager; or purchase of non-technical odds and ends
(purchase cards). It too has advantages as defined by your text:
* Speed and Responsiveness
* Understanding Unique Operational Requirements
* Product Development Support
* Ownership
In addition, they include such things as:
* More authority to organizations charged with that profit center.
* Better communication with internal customers.
* Broader responsibilities for internal users.
However, the disadvantages are many:
* More difficult to communicate among business units
* Encourages users not to plan ahead
* Operational versus strategic focus
* Too much focus on local sources–ignores better supply opportunities
* No critical mass in organization for visibility effectiveness
* Lacks clout
* Sub optimization
* Business unit preference not congruent with corporate preference
* Small differences get magnified
* Reporting at low level in organization
* Limits functional advancement opportunities
* Ignores larger organization considerations
* Limited expertise for requirements
* Lack of standardization
* Cost of supply relatively high
The perception of many customers regarding the usefulness of the purchasing operation is changing through increased use of cross-functional teams in the sourcing process and separation of strategic versus tactical activities (ordering officials for delivery orders).
The Team Approach as Part of the Organizational Structure
Driven by pressures to reduce costs and improve the bottom line in today’s cost conscience marketplace, purchasing/supply departments have, like most other functions, sought ways to streamline operations and improve efficiency. One of the approaches that have enhanced the effectiveness of the purchasing/supply management function is the use of teams. Organizations seek to combine the flexibility of decentralized purchasing and the buying power and information sharing of centralized purchasing through the use of teams–a number of people working together on a common task. Various types of purchasing and supply management teams are used, including cross-functional teams, teams with suppliers, teams with customers, teams with both suppliers and customers, supplier councils (key suppliers), purchasing councils, commodity management teams, and consortiums (pool buying with other firms) Cross-Functional Sourcing Teams consists of personnel from at least three functions brought together to achieve a purchasing or material-related task in which the team must consider purchasing/sourcing goals or decisions involving supply base management.
Frequently, you find staff from purchasing, finance, engineering and legal counsel. Teams with Supplier Participation make sense when requirements are being developed by using supplier workshops to determine marketplace capabilities. Confidentiality is the biggest obstacle to supplier participation, and teams or suppliers may have to sign a confidentiality agreement to minimize the potential effect of this obstacle. However, this is one area that seems to still be off-limits in government purchasing. Teams with Customer Participation are developed in an effort to be customer driven since customers are the ultimately consumers. Supplier Councils are teams consisting of key suppliers who participate in cost reduction initiatives such as reducing lead time, eliminating waste in the system, or finding more efficient procedures. Purchasing Councils focus on a particular commodity and are composed of purchasing managers and buyers throughout the organization. The goals of the council are to properly manage the buyer-supplier relationship and encourage continuous improvement. Consortiums are created by separate organizations that pool their requirements for common items to gain leverage with suppliers to attain lower prices and better terms and are commonly found in not-for-profit organizations, particularly educational institutions and health-care facilities.
Hybrid Organizational Structure
Hybrid organizational structure is widely used in companies to increase the overall productivity. In this article, we shall know more about the concept and its advantages in detail.
Having a proper organizational structure is essential for companies belonging to all sectors of the economy to make progress on the business front. A well planned organizational structure can lead to increased efficiency and this will reflect on the revenue and profits of the firm. Among the different types of organizational structures is a hybrid organizational structure. It has been defined as the combination of the divisional as well as the functional structures. A hybrid organizational structure has all the advantages of these structures. Knowing what is a hybrid structure is possible only when you know the meaning of divisional and functional structures separately.
Divisional Organizational Structure
The divisional organizational structure has many teams which are entirely focused on development of a single product. The best example of such a structure can be a car company which sells cars with different names. Concentration on a single product can help the company achieve perfection and better results. However, the drawback of this structure is that competing with divisions in the same company can lead to conflicts and office politics, which can affect the total output.
Functional Organizational Structure
Functional organizational structure consists of the hierarchical grouping of the employees by the higher authorities and they are supposed to report their work to a single person in the top management. The main advantage of this organizational structure is that the lines of instructions are very clear and that employees come together to perform certain tasks in the organization which results in better output. Many times, lack of communication in the groups is considered as a disadvantage of functional structure.
Hybrid Structure Advantages
Increased Efficiency
Hybrid structure consists of multiple organizational designs. It has two different organizational structures which have been combined together. The main aim behind the formation of such a structure is to improve the efficiency and manner of functioning of the company. As we all know, running an organization smoothly is not one man’s job, it requires a team of dedicated and talented professionals. These professionals should be assigned work in the right quantity and at the right time. The most important feature here is that it makes work allotment and distribution extremely easy for the senior level management. This structure lays emphasis on giving employees the work in which they are experts, to ensure that they deliver a good performance for the benefit of the organization.
Creates Unity Among the Staff Members
Hybrid organizational structure is crucial for creating a sense of unity among the employees of the organization. Such an organizational structure is useful to carry out business operations on a very large-scale. Individuals, belonging to different regions work closely with each other in a hybrid organization for attainment of set goals. Cross cultural unity has helped many small organizations become large corporations with operations in several regions.
Flexibility
This organizational structure is much more flexible as compared to the divisional and functional structures. Hybrid organizations have different product lines which gives them competitive advantage in a market which has many participants. Flexible organizational structure helps keep the relations between the senior management and junior employees cordial through consistent dialog and interaction. Also, all sorts of employee problems, grievances and doubts are easily addressed.
Decentralization of Decision-making
Decentralization of the decision-making process is very essential to make the junior level employees a part of the organization’s growth. It has been observed that the autocratic leadership process in which the management lays their rules, and when the juniors follow them without voicing their opinion, may not be favorable for organizational growth. By giving power and rights to the junior level employees to take some decisions on their own, can help build their confidence steadily.
Optimum Use of Resources
Optimum use of available resources is possible with the hybrid organizational structure. Resources are valuable and if they are put to the best use, they can help the company achieve its financial goals. Under this organizational structure, wastage of time and resources can be completely avoided.
Apart from this structure, the matrix organizational structure, functional structures, virtual structures and team structure are also well-known in the industry. Hybrid organizations are operational in both, the public as well as the private sector. Hence, it caters to the needs of government as well as private bodies which is indeed a major plus point. This structure’s implementation is a big challenge which the company management needs to take up seriously. So, we conclude that this structure, is without any doubt, the best one in today’s modern business environment.
What is a Cross-Functional Team?
A cross-functional team is simply a team made up of individuals from different functions or departments within an organization. Teams like this are useful when you need to bring people with different expertise together to solve a problem, or when you want to to explore a potential solution. For example, you might put together a team made up of people from finance, engineering, production, and procurement to come up with a solution to reduce the lead-time for a new product. One approach is for team members to be “loaned” full-time to the cross-functional team, returning to their day-to-day role once their contribution has finished. Alternatively, they may work on a part-time basis, continuing with their existing responsibilities alongside their cross-functional team-work. The most important distinction between the creation of a cross-functional team and the formation of a new department is that members of a cross-functional team maintain substantial links to their day-to-day responsibilities and to managers in their “home” department.
Note:
Projects often involve people from a variety of functions. However, projects tend to have a more formal structure, have set deliverables and timelines, and have a definite end point. A cross-functional team is more likely to be used when the team has an ongoing responsibility, or when the team is meeting for a short period of time to solve a problem.
Challenges
It’s always a challenge to create a new team, but setting up a cross-functional team has additional difficulties. For instance:
* Team members may still be doing their “day jobs,” with the same responsibilities, workload, and deadlines as before. This can lead to prioritization issues. * People might be reluctant participants, and may not be happy to take on the additional work and effort that being part of a cross-functional team often requires. (This may be true for you, too!) * It’s more difficult to set priorities, make decisions, motivate people, and manage performance when you don’t have direct authority over members of the team. * Team members may be required to use a different set of skills in a new environment. For example, a programmer who normally works alone may now be required to work with others.