Z-Source Inverter Fed Bldcmotor
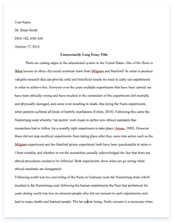
- Pages: 4
- Word count: 885
- Category: Performance
A limited time offer! Get a custom sample essay written according to your requirements urgent 3h delivery guaranteed
Order NowPerformance Analysis of Z-Source Inverter fed PM BLDC Motor Drive Vidya Sojan M.Tech Scholar, Department of Electrical Engineering, College of Engineering, Thiruvananthapuram, INDIA Email: [email protected] Abstract — This paper deals with the simulation of the closed loop operation of a Permanent Magnet Brushless DC Motor Drive system with a Z-source inverter and conventional six switch inverter, and their performance comparison. Simulation results are presented to demonstrate the performance evaluation of two inverter topologies. The comparison shows that the Z-source inverter is very promising for BLDC motor drives. Key Words-Brushless DC motor drive; Z-source inverter; hysteresis current controller; speed control.
Mrs. Lekshmi A. Senior Lecturer, Department of Electrical Engineering, College of Engineering, Thiruvananthapuram, INDIA Email: [email protected] a BLDC motor drive system fed by a Z-source inverter will have the advantages of both of them, and will be suitable for the fuel cell based electric drive systems. The output voltage of Z-source inverter can be easily controlled by controlling the shoot-through time by using space vector PWM technique [9-10]. For the sake of comparison, the dynamic and steady state performance of the Z-source inverter fed BLDC motor drive are referred to the ones of the conventional VSI fed BLDC motor drive.
This paper deals with the simulation of the closed loop operation of a BLDC motor fed by conventional six step inverter and Z-source inverter. MATLAB/SIMULINK schematic of the BLDC motor drive system is developed and the same is used for simulation. A detailed evaluation of the proposed inverter is presented in the following sections. The configuration, operating principle and control method of proposed electric drive system are described in section II.
A modeling procedure for the conventional VSI fed BLDC motor is also discussed. Section III deals with the analysis of Z-source inverter fed BLDC motor drive and design of impedance network. Computer simulations are used to verify the accuracy of the design process and the BLDC motor drive. In section IV and V, simulation studies are carried out to verify the desired performance of the proposed electric drive system. Finally, derived conclusions are presented in section VI. II. OPERATION OF BLDC MOTOR USING CONVENTIONAL VOLTAGE SOURCE INVERTER
I. INTRODUCTION Permanent Magnet Brushless DC [BLDC] motor is increasingly being used in automotive, computer, industrial, and household products because of its high efficiency, high torque, ease of control, and lower maintenance. A BLDC motor is designed to utilize the trapezoidal back electromotive force [EMF] with square wave currents to generate the constant torque [1]. The permanent magnet BLDC motor can be used in various applications such as electric vehicles where portability and efficiency are required. The conventional Voltage Source Inverter [VSI], the most commonly used type of inverter, suffers from the drawback that it cannot boost the voltage of the input source. In order to satisfy the pressing needs for a single converter capable of both voltage boosting and inversion, many new inverter topologies have been proposed in the recent past [2].
Among these new topologies, Z-Source Inverter is gaining popularity over the others mainly because it continues to employ a conventional VSI as the power converter yet with a modified dc link stage. Permanent magnet BLDC motor can be used in electric drive applications such as electric vehicles and hybrid electric vehicles along with fuel cell stacks as energy source. But the output voltage of fuel cell decreases with the increase of the output current and to solve that problem, there are two main solutions: the traditional dc/dc-boosted Pulse Width Modulation [PWM] inverter and the original Zsource inverter proposed in reference [3].
Compared with the former, the Z-source inverter has more advantages such as higher efficiency and lower cost, which is very promising for fuel cell systems due to its novel voltage buck/boost ability [4]. Various conventional PWM strategies for controlling a conventional VSI can be modified to switch a voltage type Z-source inverter [5]. The interrelated literatures [6-8] demonstrate the unique features of the Zsource inverter and its feasibility for the adjustable speed drive [ASD] systems with induction machines.
Accordingly,
A. BLDC Motor The structure of a BLDC motor is shown in Fig. 1. BLDC drive system consists of a BLDC motor, control circuit and sensor for position information. In a BLDC motor drive system position information is obtained from the Hall Effect sensor output. By knowing the position of the rotor and speed error, control circuit will generate the required PWM signals with suitable duty ratio.
Fig. 1 Structure and Equivalent circuit of BLDC motor
The modeling is based on the following assumptions: (1) The motor is not saturated. (2) Stator resistance of all windings is equal and self and mutual inductances are constant. (3) Power semiconductor devices are ideal. (4) Iron losses are negligible. The modeling equations of BLDC motor can be represented in matrix form as:
trapezoidal back EMF, current waveforms and position Hall Effect sensor signals of a three phase BLDC motor. To drive the motor with maximum and constant torque, the phase currents should be synchronized with the corresponding phase back EMF voltages. Only two phases are conducting and the other phase is inactive. TABLE I CURRENT EQUATIONS ACCORDING TO THE OPERATING MODES Modes Mode 1 Mode 2 Mode 3 Mode 4 Mode 5 Rotor position -300