Sabah Gas Terminal (SBGAST) Electrical Power Consumption
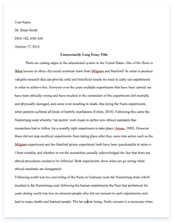
- Pages: 17
- Word count: 4147
- Category: Power
A limited time offer! Get a custom sample essay written according to your requirements urgent 3h delivery guaranteed
Order Now* To gather information on the power consumed in Sabah Gas Terminal.
* To calculate the total power consumed in Sabah Gas Terminal area.
* To learn about MicroTurbine Generator in Sabah Gas Terminal.
* To expand my knowledge on Power Generations.
* To suggest an alternative to replace MTG.
Section 2: INTRODUCTION TO SABAH GAS TERMINAL
Sabah Gas Onshore Terminal (SBGAST) is located at Kg. Gayang, around 50 km north east of Kota Kinabalu. The installations are sited on 20 hectares of costal land, conveniently accessible by road. Natural gas is piped through a 16” subsea pipeline to SBGAST from Erb-West Platform, located 65 km offshore. Sabah Gas Onshore Terminal (SBGAST) is design to process 150 mmscfd of raw gas. Product gas will pipe directly to consumers and the condensate is exported by road tankers.
Section 3: SABAH GAS TERMINAL POWER DISTRIBUTION SYSTEM
Section 3.1: Existing Electrical System Configuration:
There is no external electrical grid power supply such as SESB/TNB connection to Sabah Gas Terminal. All electrical generations are independent from the Micro Turbine Generators (MTG -501 to MTG-508) or Diesel Engine Generator (GD-7500). During the observation at site, there was an additional rental portable generator for back up. There are eight units of Micro Turbine Generators (MTG) rated at 60 kW each installed in Micro Turbine shed. One unit of 1250 kVA Diesel Engine Generator is installed in their respective sheds. All generators are connected to MCC-7600. Section 3.2: Electrical System Operation Regime:
The operating philosophy for the MTGs are on 6 + 2 basis in which 6 are running and 2 are on stand-by at any time. In the event of MTG unavailable (under maintenance or repair), the Diesel Engine Generator (DEG) or rated Portable Engine Generator (PDG) shall be put into operation to make up the difference.
Section 4: PROBLEM STATEMENT
MicroTurbine Generators (MTG) are the main power generator to supply the whole area of SBGAST. They have a total of 8 generators altogether. Each generator only generates up to 60 kW of power. Therefore in this project I am asked to study about the power generated and how is it distributed throughout the whole area in SBGAST itself. Section 5: METHODOLOGY: ABOUT MICROTURBINE GENERATORS
Section 5.1: Introduction
The Capstone C60 MicroTurbine provides electrical power generation. The Capstones C60 MicroTurbine may be configured for either Grid Connect or Stand Alone operation. The Grid Connect configure causes the MicroTurbine to source current into an energized electrical grid, and the Stand Alone configuration allows the MicroTurbine to function as a grid-isolated voltage source. Capstone C60 MicroTurbines may be used in applications requiring greater than 60 kW of required amount of power. A MultiPac grouping of MicroTurbines will function as if it were a single unit. Section 5.2: Purpose
The purpose of this section is to define the electrical performance ratings of the Capstone C60 MicroTurbine in both single unit and MultiPac configurations. This information is intended for use in the evaluations of applications for the Capstones C60 Microturbine. Section 5.3: Scope
This section defines only the electrical ratings and characteristics of the CapStone C60 MicroTurbine single unit and MultiPac. Other documentation is available for defining the ratings and characteristics of the other various MicroTurbine components.
Section 5.4: Definitions
The following table presents General Terms and Definitions used in this section.
Table 1: General Terms and Definitions
General Terms| Definitions|
A| Amp (or Ampere): The unit measurement of electric current| AC| Alternating Current: The type of power where the polarity of the current is reversed 60 times per second in the U.S and 50 times per second in Europe.| ANSI C62.45| American National Standards Institute – Low Voltage AC Power Circuits: Surge Test Guide.| ARMS| Amps Root Mean Square|
BSOC| Battery State-of-Charge|
CF| Crest Factor (CF) = IPEAK/IRMS|
°C| Degree Celsius. A temperature scale. 0 Celsius (or 0 Centigrade) is the freezing point of water (32 °F)| °F| Degree Fahrenheit. The thermometric scale on which, under standard atmosphere pressure, the boiling point of water is at 212 degree above the zero of the scale and the freezing point is 32 degree above that zero| Capstone| Capstone Turbine Corporation|
DC| Direct Current|
HP| High Pressure|
H| Henry (or henries)|
Hz| Hertz: The frequency of electrical alternations (cycles) per second. One Hz is equal to one cycle per second| IEEE 519| Institute of Electrical and Electronic Engineers: Recommended Practices/Requirements for Harmonic Control – Electrical Power Systems| IEC 61000-3-3| International ElectrotechnicalCommision: ElectronmagneticCompatibality – Part 3, Limits – Section 3: Limitation of voltage fluctuations and flicker in low voltage supply systems for equipment with rated current and less than or equal to 16 amps.| ISO| International Standards Organization|
IRMS| Current (or Amps) Root Mean Square|
I/O| Input/Output|
kVA| Thousand Volt amperes|
kVAR| Thousand volt amperes reactive|
kW| Thousand Watt|
kWh| Thousand Watt Hours|
KYZ| Option offered by Wattmeter OEM’s that provides pulse train output for power rate-of-flow| L| Stands for Inductor (as in L1 = Inductor 1).|
LP| Low Pressure|
N/A| Not applicable|
N| Whenever an expression is listed, N = the number of individual MicroTurbines within a MultiPac (where1≤ N ≤ 100)| RMS| Root Mean Square| RS – 232 Port| Defines three types of interfaces, electrical, functional, and mechanical. Idealfor the data-transmission range of 0-20 kbps/50 feet. It employs unbalancedsignaling and is used with 25-pin D-shaped connectors (DB25) to interconnectvarious components. Serial data exits through an RS-232 port via theTransmit Data (TD) lead and arrives at the destination device’s RS-232 portthrough the Receive Data (RD) lead.| RS – 485 Port| Resembles other ports except that associated drivers are tri-state, not dualstate.It may be used in multipoint applications where one central computercontrols many different devices. Up to 64 devices may be interconnected withRS-485.| TB| Terminal Board (as in TB1 = Terminal Board 1)
THD| Total Harmonic Distortion|
UL| Underwriters Laboratories|
VRMS| Volt Root Mean Square|
VDC| Volts Direct Current|
VAC| Volts Alternating Current|
Table 2: Electrical Ratings: Grid Connect
Description| Single Unit| MultiPac|
Grid Voltage Operating Range| C60: 360 to 528 VAC, (3-phase only)C65: 380 to 528 VAC, (3-phase only)| Same as Single Unit| Output Voltage Connection| 3 wire, L1, L2 and L3| Same as Single Unit| Maximum Grid Impedance| ≤ 10% inductive (814 μH) and≤ 5% resistive (0.153 ohms),Zbase= 3.07 ohms line-to-neutral| ≤ 10% inductive (814/N μH)and ≤ 5% resistive (0.153/Nohms), Zbase= 3.07/N ohmsline-to-neutral| Grid Voltage Harmonic Distortion| The grid must comply with IEEE 519. Note 1.| Same as Single Unit| Grid Voltage Balance| Within ± 2% at full load| Same as Single Unit| Grid Voltage Phase Displacement| 120(± 1) degrees| Same as Single Unit| Grid Voltage Phase Rotation| Either clockwise or counter-clockwise.Auto synchronization.
For Dual Modeapplications, the grid voltage phaserotation must be L1, L2, and L3,counter-clockwise.| Same as Single Unit| Grid Inrush Current@ Disconnect Switch Closure,(per individual unit within aMultiPac)| 24 Amps RMS| Same as Single Unit| Grid Frequency Acquisition Range| 45 – 65 Hz. Auto synchronization. TheMicroTurbine senses the gridwaveform and synchronizes to itsphases and frequency before anoutput connection is made.| Same as Single Unit| Output Power| C60: 0 (Note 2) to 60 kW HP fuel.C65: 0 (Note 2) to 65 kW HP fuel.| 0 to kW = Σ(kWMT* NMT)(Note 3)| Output kVA (@ 480 Volts)| 83.0 kVA| N*83.0 kVA|
Output Power Factor to Grid| ± 0.985 displacement PF, for loads >25% of rated load| Same as Single Unit| Output Power Slew Rate| ± 2 kW/second, minimum| ± N*2 kW/second, minimum| Output Current| 100 Amps RMS, maximum steady state| N*100 Amps RMS, maximum steady state| Output Current Harmonic Content| Complies with IEEE 519< 5% THD.| Same as Single Unit| Output Current DC Content| <0.6 Amps DC (per UL 1741)| < N*0.6 Amps DC (UL 1741)|
Note 1: Total harmonic voltage must be less than 5% (13.85 Volts RMS line-to-neutral). Also, the high frequency ripple voltage must be less than 5.5 Volts RMS line-to-neutral at frequencies greater than 3 kHz. Note 2: The minimum typical power to the grid is 1.8 kW (@ Tamb = 122°F) or 3.4 kW (@T amb = 59°F) when the Power Demand is 0 kW. For MultiPac, the typical minimum power to the grid is N* 1.8 kW (@ Tamb = 122°F) or 3.4 kW @ Tamb = 59°F).
Note 3: The total available power is the summation of the powers available from the individual MicroTurbines. kWMT = kW rating @ ambient conditions, of high pressure Capstone 60/C65 MicroTurbines NMT = number of high pressure Capstone C60/C65 MicroTurbines
Note 4: UL 1741 test-rated short circuit is 145 ARMS.
Figure 1 presents the typical Total Harmonic Current as a function of load for one Capstone C60/C65 MicroTurbine of a MultiPac in the Grid Connect mode. Figure 1. Typical Total Harmonic Current
Electrical Ratings: Stand Alone
Table 2 presents the Electrical Ratings for the Stand Alone configuration. Whenever an expression is listed. N equals the number of individual MicroTurbines which a MultiPac (where1≤ N ≤ 100). See Figure 2.
Table 3: Electrical Ratings: Stand Alone
Description| Single Unit| MultiPac|
Output Voltage Adjustment Range| 150 to 480 VAC line-to-line(1 VAC adjustment resolution)| Same as Single Unit| Output Voltage Accuracy| ± 2% of reading,(± 1% typical) line-to-neutral| Same as Single Unit| Output Voltage Stability. Time| ± 1.5% per 40,000 hours| Same as Single Unit| Output Voltage Stability Temperature| ± 0.2% over −20to +60 °C(internal temperature)| Same as Single Unit| Output Power| 0 to 80 kW HP Fuel| 0 to kW = 0.95*Σ (kW60HP*N60HP) (Note 2)| Output kVA (@480 Volts)| 83.0 kVA| N*83.0kVA|
Load Power Factor| 0 lagging to 0.8 leading| Same as Single Unit| Output Voltage Harmonic Distiortion with Linear Load| ≤ 5% THD, which complies withIEEE 519. See Figure 2.| Same as Single Unit| Output Voltage Harmonic Distortion with CF load. Crest Factor (CF) = IPEAK/iRMS| < 8% THD, IPEAK ≤ 180 Amps1.4 ≤ CF ≤ 3.0| < 8% THD, IPEAK ≤ .95*N*180Amps 1.4 ≤ CF ≤ 3.0| Output DC Voltage Content| ± 2.5 Volts DC line-to-neutral| Same as Single Unit| Output Voltage Step Load Regulation, load application or removal| < ± 20% of nominal voltage forany resistive step load ≤ 100%rated load| Same as Single Unit| Output Voltage Step Load Recovery Time| < 100 milliseconds to within± 5% of nominal voltage for≤ 100% rated load step| Same as Single Unit| Output Voltage Phase Displacement| 120 (± 1) degree @ balancedloads|
Same as Single Unit| Output Voltage phase Displacement Jittler| ± 1 degree @ balanced loads| Same as Single Unit| Output Voltage Phase Rotation| L1, L2, L3 counter-clockwise| Same as Single Unit| Output Frequency Adjustment Range| 10 – 60 Hz (0.1Hz adjustmentresolution), ± 0.05% accuracy.For integer frequency settings,the accuracy is +/- 0.005%.| Same as Single Unit| Output Frequency Regulation| 0% change for any steady stateload or transient load ≤ 100%| Same as Single Unit| Output Frequency Stability Time| ± 0.0005% per year| Same as Single Unit| Output Frequency Stability Temp| ± 0.005%, -20to +60 °C| Same as Single Unit| Output Load Current| 100 Amps RMS, maximum steady state. The maximum output current tracks the engine power derating with ambient temperature.| Amps RMS = 0.9*100*N,1≤ N ≤ 100 typical, maximumsteady state.
The maximumoutput current tracks the enginepower derating with ambienttemperature.| Output Load Crest Factor (CF)| 1.8 maximum @ 100 AmpsRMS with CF=180/IRMSfor loads < 100 Amps RMS| 1.8 maximum @ AmpsRMS = 0.9*100*NCF=0.9*N*180/IRMSfor loads < 0.9*100*N AmpsRMS| Output Instantaneous Load Current| 180 Amps peak, maximum| 0.9*N*180 Amps peak. Maximum| Overload Capacity (% of full power output per individual unit in a MultiPac)| 150%, 10 seconds; 125%, 30seconds; 110% 60 seconds(BSOC >70%). Underconditions of 480 Volts AC and1.0 PF, available power issubject to temperature-relatedover-current limits.| Same as Single Unit| Output Fault Current| 145 Amps RMS, maximumsymmetrical and asymmetrical| N*145 Amps RMS, maximum symmetrical and asymmetrical| Output Load Cycle Period| -| Same aas Single Unit|
Single Phase Loading (per individual Micro Turbine within the MultiPac)| 25 kW line-to-neutral maximum steady state| Same as Single Unit| Load Unbalance among the 3 phases (Per individual unit within the MultiPac)| 25 kW maximum. A typical arrangement of unbalanced loads is 30kW, 5 kW and 5 kW per phase, per unit respectively.| Same as Single Unit| Surge Voltage| ANSI 62.45, ± 4 kV standard,± 6 kV available. A surgesuppressor must be added toachieve this requirement.Contact Capstone.| Same as Single Unit| Grounding.
Consult the Electrical Installation Technical Reference for details| Neutral must be solidlyconnected to earth groundin a single location.| Same as Single Unit| Motor Start, Across-the-line| Motor inrush current< 127 Amps RMS. This currentlimit must not be exceeded atany time during acceleration tofull speed.| Motor inrush current< 0.9*N*127 Amps RMS. Thiscurrent limit must not beexceeded at any time duringacceleration to full speed.| Motor Start, Ramp Voltage and Frequency| 127 Amps RMS: maximumstarting current at anyfrequency and voltage. Thiscurrent limit must not beexceeded at any time duringacceleration to full speed.| 0.9*N*127 Amps RMS,maximum starting current atany frequency and voltage.This current limit must not beexceeded at any time duringacceleration to full speed.
Note 1: Operation at less than 0.8 leading power factor is possible if the total capacitive load is less than 50 kVAR.
Note 2: Different models of MicroTurbines may be mixed within a MultiPac. The total available power is the summation of the powers available from the individual MicroTurbines. kWMT = kW rating @ ambient conditions, of high pressure Capstone C60/C65 MicroTurbines NMT = number of high pressure Capstone C60/C65 MicroTurbines
Figure 2 presents the typical output voltage (line-to-Line) Total Harmonic Distortion (THD) as a function of Linear Resistive Load for the Capstone C60/C65 MicroTurbine.
Figure 2. Typical Output Voltage Total Harmonic Distortion
Section 5.5.1: Power
The CPC-100 requires 9 to 30 VDC. The power may be derived from the MicroTurbine or an external DC supply.
Section 5.5.2: Nominal Net Power Output, Efficiency, and Other Parameter Values Calculation
In order to calculate the expected net power output, proceed as follows:
* Look up the estimated power using Temperature Derating table. * Subtract parasitic loads (Fuel Gas Booster, Battery charging). * Apply ambient Pressure/Elevation Derating
* Apply Back Pressure Derating
* Apply Inlet Pressure Loss Derating.
Example:
Conditions:
C60 Grid Connect, 4.5 kW loss from Fuel Gas Booster, ambient temperature of 75 °F,and 800 ft. above sea level.
Calculations:
Power based on temperature = 60.0 kW
Fuel Gas Booster Loss = 4.5 kW
Elevation Derating = 0.971
Expected Power = (60-4.5) x 0.971 = 53.89 kW
Nominal net power output and efficiency versus ambient temperature at sea level for the Model C60 MicroTurbine operating on high-pressure natural gas (B Range) fuel is presented in Table 3. These values are estimated from nominal performance curves.
Table 3: Nominal Net Power Output and Efficiency versus Ambient Temperature at Standard Sea Level Pressure
Table 4. Nominal Net Power Output and Efficiency versus Ambient Temperature at Standard Sea Level Pressure
Table 5. Nominal Net Power Output and Efficiency versus Ambient Temperature at Standard Sea Level Pressure
Temperature Derating (continued)
Nominal net power output and efficiency versus ambient temperature at sea level for the Model C60 MicroTurbine operating on natural gas (B range) fuel is presented in Figure 1.
Figure 3: Nominal Net Power Output and Efficiency versus Ambient Temperature at Sea level Section 5.6: Electrical Connections: Stand Alone
If the Capstone MicroTurbine is equipped with the Stand Alone option, the operator must supply the electrical cable and switchgear through which the Capstone MicroTurbine delivers its output power. The cabling and switchgear must be capable of safely handling the maximum potential loads, and must meet all applicable local and national regulations. It is essential that the owner/user consult all of the applicable codes and standards before electrically wiring the MicroTurbine. A qualified electrician may be required to do the work. The electrical connection terminal block for the MicroTurbine can be found in the Power Bay located at the rear of the enclosure.
Section 5.6.1: Stand Alone Loads
Stand Alone loads may be connected in any combination of line-line or line-neutral, while respecting the maximum current and voltage ratings as described in the Model C30 Electrical Technical Reference (410000) and the Model C60 Electrical Technical Reference (410001). Notice that in Stand Alone systems, the MicroTurbine(s) neutral must be solidly connected to ground at a single point.
Section 5.6.2: Voltage
The output voltage from the MicroTurbine may be programmed from 150 to 480 volts AC, phase-to-phase, and 10 to 60 Hz. Output power capabilities are reduced at the lower voltage levels, based on the operational current limits.
Section 5.6.3: Phase Rotation
The output voltage/current phase rotation is counterclockwise, as in L1 to L2 to L3. Notice that improper phase rotation connections can damage the connected loads. Capstone cannot be held responsible for equipment damage caused by improper connections. It is the operator’s responsibility to verify the proper phase connections between the MicroTurbine and the load(s).
Section 5.6.4: Stand Alone Transformer Applications
For Stand Alone applications, power transformer(s) will be needed for loads that require voltages different from the programmed MicroTurbine Stand Alone voltage set point. Refer to the Stand Alone Operation Technical Reference (410028) for details on the voltage and protective set points used for Stand Alone operation.
Section 5.6.5: Load Circuits
The MicroTurbine output consists of three phases and a neutral circuit. These may be used in any combination, limited only by current limits on each phase, as described in the Model C30 Electrical Technical Reference (410000) and the Model C60 Electrical Technical Reference (410001).
The nominal Stand Alone voltage setting is available between any two phases. Single phase and/or unbalanced loads can be accommodated, respecting the current and power limits previously noted. Notice that the MicroTurbine
Neutral must always be grounded. Section 5.6.6: Load Capacity
The MicroTurbine output is current limited. The MicroTurbine can operate loads with any power factor, so long as current limits are not exceeded. The current (I) consumed by the load(s) is a function of real power (Watts), volts (V) and the power factor (PF). I= W3×V ×PF
The allowable power factor (PF) will be a function of the real load and the maximum phase current. Power derating curves for ambient temperature and elevation should be considered when determining real power (Watts). Refer to the Model C30 Performance Technical Reference (410004) and to the Model C60 Performance Technical Reference (410005) for additional details. For example, with a total 30 kW load operating at 480 Volts AC with a current limit of 46 ARMS per phase, the lowest allowable power factor (PF) is as follows: 300003×480 ×46=0.78
Operating at 376 volts AC, the lowest allowable power factor (PF) is as follows:
300003×376 ×46=1
Operating voltages lower than 376 volts AC will consequently reduce the total available output power of the MicroTurbine according to the following: W = 46× 3 ×V × PF
Section 5.6.7: Input Impedance Calculations – Examples
Refer to the Model C30 Electrical Technical Reference (410000) and the Model C60 Electrical Technical Reference (410001) for input impedance requirements. Three examples of the total electrical input impedance calculations which detail the values considering the MicroTurbine output looking towards the utility are provided as follows:
Example 1: Model C30 – Considering 1 MicroTurbine
Total Impedance for all conductors: ZL = 0.5%, ZR = 1.0%
ZL (Total) = 5.6%(30/45) + 6.4%(30/45) + 5%(30/60) + 0.5% = 11% (Value exceeds acceptable limits)
ZR (Total) = 1.7%(30/45) + 1.9%(30/45) + 1.6%(30/60) + 1% = 4.22% (Value is within acceptable limits)
Example 2: Model C60 – Considering 1 MicroTurbine
Total Impedance for all conductors: ZL = 0.5%, ZR = 1.0%
ZL (Total) = 5.6%(60/75) + 6.4%(60/75) + 5%(60/100) + 0.5% = 13.1% (Value exceeds acceptable limits)
ZR (Total) = 1.7%(60/75) + 1.9%(60/75) + 1.6%(60/100) + 1% = 4.85% (Value is within acceptable limits)
Example 3: Considering 3 MicroTurbines
Total Impedance for all conductors: ZL = 0.5%, ZR = 1.0
MicroTurbine #1 (30 kVA):
ZL (MT1) = 5.6%(30/45) + 7.2%(120/500) + 5%(120/2000) + 0.5% = 6.3% (Value is within acceptable limits)
Note: In these calculations, the number 120 represents the sum of the MicroTurbine outputs (30+30+60) ZR (MT1) = 1.7%(30/45) + 1.8%(120/500) + 1.3%(120/2000) + 1% = 2.7% (Value is within acceptable limits)
MicroTurbine #2 (30 kVA):
ZL (MT2) = 5.6%(30/45) + 7.2%(120/500) + 5%(120/2000) + 0.5% = 6.3% (Value is within acceptable limits)
ZR (MT2) = 1.7%(30/45) + 1.8%(120/500) + 1.3%(120/2000) + 1% = 2.7% (Value is within acceptable limits)
MicroTurbine #3 (60 kVA):
ZL (MT3) = 4.3%(60/112.5) + 7.2%(120/500) + 5%(120/2000) + 0.5%= 4.9% (Value is within acceptable limits)
ZR (MT3) = 1.4%(60/112.5) + 1.8%(120/500) + 1.3%(120/2000) + 1%= 2.3% (Value is within acceptable limits)
Section 6: Data Gathering
Below is the power consumed by SBGAST since January 2011 till September 2012
based on the SBGAST Electrical Technician Daily Log: YEAR| MONTH| MICROTURBINE GENERATOR (MW)| ENGINE DIESEL GENERATOR (MW)| PORTABLE DIESEL GENERATOR (MW)| TOTAL (MW)| 2011| JAN| 277.45| -| -| 277.45|
| FEB| 291.06| 1.35| -| 292.41|
| MAR| 282.05| -| -| 282.05|
| APR| -| 2.0| 482.05| 484.05|
| MAY| -| 291.82| 151.23| 443.05|
| JUNE| -| 427.57| 66.66| 494.23|
| JULY| -| 16.88| 246.59| 263.47|
| AUG| -| 16.88| 271.67| 288.55|
| SEPT| -| | 214.67| 214.67|
| OCT| -| 23.95| 193.38| 217.33|
| NOV| 502.77| 0.86| 60.29| 563.92|
| DEC| 397.81| -| -| 397.81|
2012| JAN| 357.66| 0.68| -| 358.34|
| FEB| 345.73| -| -| 345.73|
| MAR| 389.36| 11.15| -| 400.51|
| APR| 381.16| 13.06| -| 394.22|
| MAY| 444.61| 18.2| -| 462.81|
| JUNE| 447.4| 19.54| -| 466.94|
| JULY| 384.75| 52.12| -| 436.87|
| AUG| 816.71| -| -| 816.71|
| SEPT| 255.19| 126.8| -| 381.99|
Below is the power consumed by SBGAST based on the data instructed in the P&ID::: BUSSES| ELECTRICAL APPLIANCES| POWER CONSUMPTION (kW)|
RIGHT| HVAC PANEL FEEDER #1 FOR ADMIN BLOCK| 100|
| PM – 35208 CONDENSATE EXPORT PUMP B| 15|
| PM – 25508 OFFSPEC REC. PUMP| 5.5|
| PM – 67108 DIESEL TRASFER PUMP| 4|
| WELDING RECEPTACLES AT WATER TREATMENT AREA| 30|
| KM – 5400A A75IR COMPRESSOR| 75|
| CDF – 6510 CDF EFFLUENT WATER PUMP| 5.5|
| SM – 6560E IGF DEFURATOR SKIMMING PUMP| 0.37|
| E – 3460B CONDENSATE AIR COOLER FAN| 3.7|
| SO – 02 WELDING RECEPTACLES AT FIREWATER PUMP AREA| 30| | MOV PANEL FOR SCRAPPER TRAP AREA| 20|
| PM – 6515 CDF – OFFSPEC WATER PUMP| 5.5|
| PM – 6595 OIL RECOVERY SUMP PUMP| 3|
| PM – 6700 REFILLING PUMP| 0.75|
| SO – 03 WELDING RECEPTACLES AT COND. LOADING AREA| 30| | PM – 6536B CPI EFFLUENT WATER PUMP| 3|
| LIGHTING/POWER DIST. BOARD ADMIN BLDG.| 50|
| PERIMETER AND COMPOUND LIGHTING DIST. BOARD| 100|
| SM – 6560A IGF DEFURATOR| 5.5|
| SM – 6560B IGF DEFURATOR| 5.5|
| AUX. POWER DIST. BOARD | 30|
| LIGHTING/POWER FOR CONTROL BUILDING DIST. BOARD| 50|
LEFT| PM – 3550A OFFSPEC REC. PUMP| 5.5|
| PM – 6710A DIESEL TRANSFER PUMP| 4|
| SO – 04 WELDING RECEPTACLES AT PROCESS AREA| 30|
| KM – 5400B AIR COMPRESSOR| 75|
| PM – 6555 IGF UNIT FEED PUMP| 5.5|
| E – 3460A CONDENSATE AIR COOLER FAN| 3.7|
| SM – 6560C IGF DEFURATOR| 5.5|
| SO – 05 WELDING RECEPTACLES AT SLUGCATCHER AREA| 30|
| PM – 6535A CPI EFFLUENT WATER PUMP| 1.5|
| SM – 6560D IGF DEFURATOR| 5.5|
| SO – 06 WELDING RECEPTACLES AT GAS METERING AREA| 30|
| LIGHTING / POWER DIST. BOARD FOR WORKSHOP| 100|
| PM – 6420 DRAIN PIT SUMP PUMP| 1.5|
| SM – 6560F IGF DEFURATOR SKIMMING PUMP| 0.37|
Note: Spare Starters, Spare Feeders and other electrical appliances that are not operating anymore such as condensate electrical heaters are excluded.
Section 7 – Conclusion
From the tabulated data, it shows that SBGAST normal total power consumption is in the range of 200kW up till 300kW per day. Power consumption for the Fire Water Pump is excluded since it is only being used once in a week to test-drive the Fire Water Pump. If the Fire Water Pump is included, the total power consumed is about 435kW at the time when the Fire Water Pump is operating. A similar peak in electrical consumption is also observed during air compressor switchover activities. Each MTG only produces power up till 60kW per generator and the efficiency of the generator is 70% of its maximum power produced. So, the total power of combined 6 MTGs (based on operating philosophy of 6 + 2) is approximately 360 kW (running full load). Even if all of the MTG is operating at one time, the total power produced is 364kW with an efficiency of 70%. This shows that on normal basis, the power generated is sufficient but on emergency case or for any future upgrading, 6 MTGs will not be enough to adequate the whole area of SBGAST. Furthermore, for the Fire Water Pump to operate, the starting point of its generator needs 3 times more power than the normal operating point.
Section 8 Recommendation
It is highly recommended to review SBGAST Consumption in account to normal and abnormal situation to determine whether the existing power generator is adequate enough or not. This will determine whether or not SBGAST needs to upgrade or replace its existing generator or operating philosophy.
Section 9: Reference
Sabah Gas Terminal Piping and Instrumentation Diagram
Sabah Gas Terminal Operation Procedure Manual
Sabah Gas Terminal Electrical Equipment Log
DOSSIER
http://www.capstoneturbine.com/
http://en.wikipedia.org/wiki/Gas_turbine