Power Coating Adhesion and Outgassing on Galvanized Steel
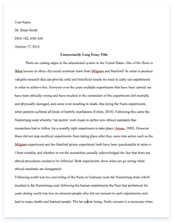
- Pages: 3
- Word count: 651
- Category: Power
A limited time offer! Get a custom sample essay written according to your requirements urgent 3h delivery guaranteed
Order NowI am contemplating powder-coating some hot-dip galvanized steel to further increase its corrosion protection. I have heard some rumors regarding the adhesion of powder coatings on galvanized steel. Apparently the adhesion is compromised due to the zinc coating outgassing. Is there any truth to this? Is there anything I can do to prevent outgassing of the zinc coating? lightly-acidic solution will remove oxides from the surface as well as slightly etch the steel surface, providing a better surface profile for top coating to adhere to. Proprietary solutions are available that are designed to work effectively on galvanized or other zinc surfaces.
ASK DR. GALV
Yes, outgassing of the zinc coating can occur when applying a powder coating over galvanized steel, which could potentially affect the adhesion and continuity of the coating. However, it can be prevented if the proper surface preparation techniques are used in conjunction with good powder application practices.
Pre-baking in a drying oven can also reduce the potential for the The key to achieving good adhegalvanized coating to outgas. This sion between powder coatings and process will aid in the expulsion of galvanized steel is surface preparaany trapped air or water in the tion. The surface must be entirely coating as well as ensure that the free from zinc oxides prior to powsurface of the steel is free from der coating. Any zinc, or other any moisture. The pre-baking metal oxides, that remain on the oven should be operated at higher surface of the galvanized steel can temperatures than the curing oven; potentially retain air or moisture. this temperature is typically 55 F Upon heating during the curing (30 C) higher than the curing Pipes color-coded using powder coating; stages of the powder application, oven. If the galvanized steel is run a common application. the oxides may release water vapor through a phosphate wash prior to or air, which can expand and penetrate the powder coating, powder coating, it is recommended that the pre-bake oven causing blisters or voids. temperature not exceed 535 F (280 C). Higher temperatures will deteriorate the thin phosphate coating, convert
The galvanized coating may also release gas due to trapped ing it into a powdery substance that could affect adhesion. air or water in the galvanized coating. Water or air may be able to penetrate small crevices within the outermost layer The cure oven temperature should be operated as low as of the zinc and become trapped. When air or water possible to further reduce the potential for outgassing. become heated during the curing stages of the powder Best results are achieved with lower oven temperatures coating process, they can release through the powder coat- and longer times as opposed to higher temperatures with ing in the form of gas to form a small crater or blister. shorter times. Not only will the lower temperatures inhib
To reduce the potential for outgassing, it is essential to remove any surface oxidation with a light sweep blast and/or chemical cleaning.
A light sweep blast will clean off any metal oxides that have developed on the surface as well as open up surface cavities that have trapped air. Sweep blasting will also increase the surface profile of the steel. This promotes good adhesion between the steel and the powder coating. In conjunction with a sweep blast — or as a stand-alone treatment — a phosphate wash treatment can be employed to remove surface oxidation. This it gassing, but the longer curing times might lead to the resealing of any craters that may have formed. As the techniques for surface preparation and powder application are refined, the application of powder coatings over galvanized steel is becoming increasingly popular. The corrosion protection provided by this duplex system will extend the life of the galvanized coating by many years, and will allow the galvanized coating to take on many different appearances.