Material Handling System in Fms
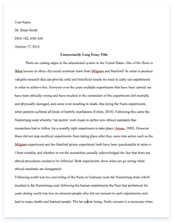
- Pages: 16
- Word count: 3891
- Category: Performance
A limited time offer! Get a custom sample essay written according to your requirements urgent 3h delivery guaranteed
Order NowMaterial handling equipment selection is vital in the design of an effective and efficient flexible manufacturing system (Kulak*, 2005). There are many factors to consider when designing MHS system. A properly designated MHS would be able to decrease manufacturing lead times, increase efficiency of material flow, and improve facility utilization and increase productivity (Kulak*, 2005). According to (Sule, 1994 ) material handling cost accounts for 30-70% of total operating cost, hence it is crucial to determine the best option for MHS. However, different MHS component would have their specific advantages and disadvantages, and there is no absolute formula in determining the type of MHS to be used, and the vast amount of variables to be consider leads to complexity while designing the MHS system.
The sole objective of this review paper is to explore various methods used during the designing of MHS system to be used in manufacturing plant, and also relating human factors role and influence in implementing successful MHS system. These methods apply various mathematical modelling and decision trees to simplify multi variables of MHS components. Various methods would be then laid out and the strengths and weakness of each of these methods would be visited.
Types of MHS
Material handling system is an automated system that assists and transfer material in the manufacturing line. It functions as a continuous, intelligent system that load raw materials to CNC machines, interconnecting the in process product to other machines for additional processes, transfer it to inspection machine for quality surveillance and finally unloading it into automated Storage and retrieval system (AS/RS) . Material handling equipment commonly categorised as industrial trucks, conveyors, Automated guided vehicles, cranes, storage/retrieval system, and robotic arms.
Journal 1: A decision support system for fuzzy multi-attribute selection of material handling equipments
Author: Osman Kulak
In this paper, the decision support system (FUMAHES) is thoroughly dissected and discussed. (FUMAHES) is a method used for selection of material handling equipment based on the requirements and rules set by the designer. FUMAHES is a type of expert systems in which the program consists of a set of modular chunks, known as rules, frame, objects or scripts. The information is stored in repository known as knowledge base. FUMAHES is developed to solve the MHS integration prior to implementation.
It is used to simplify the selection process, to choose the most appropriate MHS based on the rules set by designer. The rules and sets are basically derived from the immediate specification of the production type, usually the width of the belt conveyor, the weight of the product, and many other important rules. FUMAHES system is created using Arity Prolog. FUMAHES structure consists of detailed MHS information module (IM), axiomatic design and principles. In the database, the material handling system information is subdivided into groups of industrial trucks, conveyors, automated guided vehicles, cranes, industrial robots and storage retrieval systems. FUMAHES has a database of up to 40 move equipment types and six storage equipment types along with their performance criteria. The category and types of MHS are shown in table 1.
FUMAHES is created to overcome the problem faced when only axiom approach is used. In axiom approach, the system will not generate proper result if any of its required rules or variable is unknown. FUMAHES integrate both crisp and fuzzy criteria allowing it to be advantageous compare to other multi attribute approach. The integration of both fuzzy and crisp criteria allows the software to continue to analyse and determine the most proper MHS to be used even if the rules given are incomplete.
In this program, user inputs are required for equipment variables. Some of the input required includes cost and technical characteristics. The cost category includes fixed and variable cost pet hour where else technical category consists of conveyor speed, item width, item weight and flexibility. Once entered, the program will find the most proper equipment from the database of MHS equipment. Finally when the alternatives of eligible equipments are shortlisted, the software will rank the eligible equipment based on economic cost. In the evaluation and decision making process, alternatives are considered based on both complete and incomplete information
In short, the FUMAHES decision support system is a versatile system to be used to determine the type of MHS component to used, as it considers both technical and economic aspects during the selection process. The system is advantageous because it is able to integrate multi attribute decision making effectively through aggregate performance scores. Finally it is also a critical advantage feature of FUMAHES to be able to determine the best alternatives with limited data. However the existence of unknown variable in analysis might mislead the software to choose a less desirable MHS equipment. The system also needs to be consistently updated, so that the latest MHS equipments is included into the database.
The figure below shows the flow chart of the FUMAHES expert system
Journal 2: ICMES Intelligent Consultant System for Material Handling Equipment Selection and Evaluation Author: Yang Byung Park
The structure of ICMES system consists of 4 modules such as a) A knowledge base to select an appropriate equipment type b) A multicriteria decision making procedure to choose the most favourable commercial model c) A database to store the list of commercial models of the equipment types with their specifications
d) Simulators to evaluate the performance of the equipment model ICMESE is a type of expert system environment. It is developed to resolves the limitations of the existing expert systems for MHS that failed to integrate the factors that affect the overall productivity of MHS system. ICMESE focuses on the movement, storage and warehousing of materials factors. ICMESE is executed in VP-Expert system environment. A total of 50 types of MHS were included into the knowledge base. It is then categorised into two groups based on their functions, move equipment and storage equipment. Move equipment| Storage equipment|
Pipes| Bulk storage systems|
Conveyors| Rack systems|
Industrial trucks| Automated storage and retrieval system (AS/RS)|
Monorails| |
AGVs| |
Robots| |
cranes| |
In this system, decision tree method is used to solve the analysis. Decision tree approach is used rather than just merely creating a huge knowledge base to identify the most appropriate equipments for each unique MHS problems. This is because creating such huge knowledge base would be impractical as the number of combination can be up to hundreds. Decision tree method also reduces memory and time resources, as it only considers attributes that are relevant to the selection of equipments, rather than processing entire multi attribute that are not immediately connected to the current decision making.
By consistently narrowing the searching requirement by looking at a chunk of decision attributes at every single time, and omitting the attributes that do not meet the requirement, hence the system has the advantage of shortening the search time considerably. In the final decision where there were multiple alternatives, the best alternative would be chosen based on rough economic estimation of capital cost and operating cost. However if there is no plausible alternatives, the system will generate an error message.
In the multi criteria decision making procedure (MCDM), was developed to choose the most favourable commercial equipment model. The (MCDM) consists of two procedures, a screening process and an analytic hierarchy process (AHP). In the first stage, MHS equipments that do not meet the critical and direct specifications inputted by the user will be eliminated immediately from further consideration. In the second stage, AHP is applied to determine the best alternative among commercial models screened in the first stage. AHP is suitable because of its ability to structure complex multi criteria problem into hierarchically state.
This ICMESE is the first attempt to develop a knowledge based expert system solely for MHS selections that considers the analysis in an integrated way. However this paper failed to do a comparative summary with available known systems because of the lack of literature. Hence it is still premature to support or vice versa since there is lack of real meaningful comparison. Further improvement and research is required to further improve this system and it is recommended that this system available to be tested under industrial situations and to compare the results with other known systems. However the system had its drawbacks. The decision tree modelling still requires further improvement to enhance its capability and also the commercial model database should be enlarge and expanded so that more commercial system available for considerations.
Journal 3: Improving distribution operations: Implementation of material handling systems Author: Satya S. Chakravorty
This is a unique paper because in this discussion, author was looking at the aspect of human factor and their integration capability throughout the implementation period. Factors such as human resource training greatly affect the success in implementing the right MHS system. This paper discuss at length about the issues in integrating effectively both human factors and technical equipments at different phase in order for them to operate at optimal level. Hence proper work design and environment is thoroughly discussed in this section. Basically there are three stages during the implementation of MHS. In the first stage both human and technical problem exist, but human problems were the dominant issue in the implementation due to various factors. In this stage the main skill required is conflict management. In the second stage, human problem were loosely addressed, leaving technical issues that causes inconvenience to the implementation. At this stage, formal problem solving technique must be in place to resolves these standing issues.
Finally in the third stage, both human and technical issues were improved and the material handling system begins to perform at optimal level. In stage 1, there is a need for group member to understand what is expected of them and how they fit into the rest of the team. Generally in the initial stage group members show general respect to each other and there is also general respect in formal and informal leadership. However, as time progresses, members begin to compete and challenge leadership roles, creating interpersonal conflict. The friction causes decline in honest social interaction. Sometimes conflicts arise due to functional differences that exist among one another. Some experience workers felt losses of control as their previous role were partially taken up by automated components, creating a perception their acquired experience useless or redundant. During the initial implementation period, frictions arise between experience workers and inexperience workers but were resolve diplomatically through action of the supervisor.
At this stage, effective conflict management becomes an important asset in improving communication, reinforcing positive behaviour and clarifying procedures. A proper conflict resolution would clarify conflicting issues, reinstate order and stabilise the atmosphere so that members could work together cohesively. In this phase, the role of supervisor is very important. He must be competent to be able to resolve complains diplomatically, and sometimes when there are no agreeable decision among squabbling workers, he must be firm to decide a rational unilateral decision so that the operation could continue to function. In stage 2, once the members understand their roles and position, they are now more prepared to address technical issues and have a clearer vision when encountering technical conflict when following routine procedures.
Technical issues can only be effectively address in this stage because human conflicts are somewhat had been solved, allowing team members to become more task orientated and objective when addressing technical and procedural issues. In this phase, processes include identification of problems, gathering information, generating solutions, evaluating solutions and implementing solutions. Workers were also had certain level of experience to deal with the situation and offering valuable solutions to the operational team. In the final stage, the stage 3, team members would already be capable of resolving interpersonal conflict among one another and also effective in addressing technical and procedural issues, creating an effective environment in the plant. Below is the chart to show the different stages that happens during MHS implementation.
In conclusion, during the implementation of MHS system, it has to go through three overlapping transitional stages before it began to perform at optimal level. The stages must be well managed to reaped maximum benefits of implementation benefits. In the first stage conflict management skill was critical as human factor were the dominant problem. In the second stage, the human problems improved while the technical problem persisted, thus problem solving skill were critical. Lastly in the third stage, both human and technical problems improved considerably allowing the plant to operate at optimal level. The author states that the duration of each stages varies, depending on the types of industry, the corporate culture before the implementation, the willingness of the team to change and the competency of first line managers. Hence it is up to the first line manager to determine and observe which stage the operation team is in, and what should they be focusing in to be effective.
Journal 4: A Hybrid Fuzzy Knowledge-Based Expert System and Genetic Algorithm for efficient selection and assignment of Material Handling Equipment Author: S. Hamid L. Mirhosseyni *, Phil Webb
The aim of this paper is to solve the problems of material handling equipment (MHE) selection and assignment by using the hybrid approach of simulation. Although there are many researches in this area, but vastly of them are concentrate in the problem of selection and only a few are developing solution for both the selection and assignment problem. In addition, the researches up until now are providing not so practical solution due to: (1) oversimplified and unrealistic assumption used, (2) fail to include some effective attribute, (3) inefficient objective definition, i.e. only considering investment and operating cost, and lastly (4) overlook the fuzzy nature of the problems. In order to solve the selection and assignment problem in MHE efficiently, Mirhosseyni & Webb (2009) use a combination of hybrid fuzzy knowledge-based expert system and genetic algorithm methods. Before that, there are some problems needed to be solved.
Due to huge range of brands and models of the MHEs in the market now, it is impossible for the authors to include all of them, so they have chosen those equipment types that are only listed in the “Inter-Departmental Handling of Discrete Parts” sub group. Besides that, this paper also includes 21 attributes in the simulation in which six of them (i.e. weight, size, direction, distance, transfer frequency and clear height) are categorized as fuzzy attributes as numeric values can be assigned to them. In addition, extra information named lines, directions and distances between workplaces that based on users’ opinion and real condition are also included together the attributes in simulation. There are two phases involved in solving the problems of MHE selection and assignment in this paper. In the first phase, MHE selection problem is tackled by using the fuzzy expert system which built based on crisp rules and fuzzy rules. The system is used to identify a list of most appropriate MHE types with their respectively assigned factors for the handling operation.
In the phase two, genetic algorithm is used to search through the solutions from the phase one to find some optimum solutions for assignment problem. In order to improve the accuracy of the results obtained, the simulation is run for 10 times for the population size of 20 which generate 200 result quantities. Moreover, the method used in this paper is also compared with other similar domain of work done by Hassan, Hogg and Smith (1985), Welgama and Gibson (1995) and Cho and Egbelu (2005) to reveal its effectiveness. In the end, the results generated from this paper not only can be used as a reference in designing a material handling system, the simulation software designed in this paper can also provides domain of knowledge for the engineers to solve the selection and assignment problems in MHE.
Journal 5: Indicators for measuring performances of morphology and material handling systems in flexible manufacturing systems Author: Olivier Devise*, Henri Pierreval
The objective of this paper is to study the existing and new performance indicators of the pair morphology-material handling system (MHS) in helping to ease the designers in designing a flexible manufacturing system (FMS). The reason of studying the morphology and MHS in pair is due to the authors argues that there is a strong independence relationship between both of them. In the first part of this paper, the author introduces the problems faced in manufacturing systems during the time of this study. Besides, the commonly used morphology and MHS in FMS are also introduced. There are three indicators being studied in this paper, i.e. (1) the operational indicator, (2) the strategic indicator, (3) the economic indicator and the newly introduced (4) flexibility indicator. The operational indicator is classified as efficiency measurement of the operation activities of the studied systems, for example the utilization rate of the system.
The second indicator is strategic indicator, which, it is defined as the adaptability of the system toward producing new product or in other word the system’s flexibility. Lastly, the economic indicator is the financial measurement such as the purchasing cost, operating cost or the maintenance cost. Three types of pair morphology-MHS systems are chosen by the authors to study their respective performance indicators, where each system has their own features and setups. All three systems are initially subjected to produce three products (A, B, and C) and later on a new product D is introduced to the systems to be tested for the flexibility. Simulation software called ARENA is used in this paper to simulate the mathematical equations of the indicators formulated by the authors. The indicator results of each system tabulated in this paper can help the designers to design a suitable FMS system for an organization with fewer troubles. In addition, the results can also be used in as decision support system by an organization’s top management.
Discussion
Journal 1
In short, the FUMAHES decision support system is a versatile system to be used to determine the type of MHS component to used, as it considers both technical and economic aspects during the selection process. The system is advantageous because it is able to integrate multi attribute decision making effectively through aggregate performance scores. Finally it is also a critical advantage feature of FUMAHES to be able to determine the best alternatives with limited data. However the existence of unknown variable in analysis might mislead the software to choose a less desirable MHS equipment. The system also needs to be consistently updated, so that the latest MHS equipments is included into the database.
Journal 2
This ICMESE is the first attempt to develop a knowledge based expert system solely for MHS selections that considers the analysis in an integrated way. However this paper failed to do a comparative summary with available known systems because of the lack of literature. Hence it is still premature to support or vice versa since there is lack of real meaningful comparison. Further improvement and research is required to further improve this system and it is recommended that this system available to be tested under industrial situations and to compare the results with other known systems. However the system had its drawbacks. The decision tree modelling still requires further improvement to enhance its capability and also the commercial model database should be enlarge and expanded so that more commercial system available for considerations. Journal 3
In conclusion, during the implementation of MHS system, it has to go through three overlapping transitional stages before it began to perform at optimal level. The stages must be well managed to reaped maximum benefits of implementation benefits. In the first stage conflict management skill was critical as human factor were the dominant problem. In the second stage, the human problems improved while the technical problem persisted, thus problem solving skill were critical.
Lastly in the third stage, both human and technical problems improved considerably allowing the plant to operate at optimal level. The author states that the duration of each stages varies, depending on the types of industry, the corporate culture before the implementation, the willingness of the team to change and the competency of first line managers. Hence it is up to the first line manager to determine and observe which stage the operation team is in, and what should they be focusing in to be effective.
Journal 4
The author compared with other similar researches to reveal the effectiveness of his methods, which many research paper failed to do so. From the comparison the author was able enhance the method and included some effective attributes that made his research work standout.
Journal 5
Morphology and MHS in FMS are treated as a single factor in this study instead of two independent factors as they both are strongly dependence. The indicator study in FMS helps to ease the designers’ work in designing the suitable FMS and at the same time can be used as a supporting tool in the decision making for top management. However three types of systems seem too little for the industry, should include more in the future.
Conclusion
Material handling system is vital in providing the flexible manufacturing system an automated connectivity system to the entire process. We had been observing the trend that designers had been trying to solve the complexity of choosing the MHS set with expert system. Research mainly based on using database system which stores huge amount of data and specification of commercial MHS equipments. This is because using solely the capacity and experience of human designers alone is not enough. However it is also important to note that while the technical specifications and design is crucial for an efficient system, human factor must be considered too. During the implementation, both to first line manager and staff must be adequately trained. First line manager must also possess conflict management skills to overcome conflicts arises among team members.
References
Devise, O., & Pierreval, H. (2000). Indicators for measuring performance of morphology and material handling systems in flexible manufacturing systems. International Journal of Production Economics, 64, 209-218.
Cho, C., & Egbelu, P. J. (2005). Design of a web-based integrated material handling system for manufacturing applications. International Journal of Production Research, 43(2), 375-403.
Hassan, M. M. D., Hogg, G. L., & Smith, D. R. (1985). A construction algorithm for the selection and assignment of materials handling equipment. International Journal of Production Research, 23(2), 381-392.
Mirhosseyni, S. H. L., & Webb, P. (2009). A Hybrid Fuuzy Knowledge-Based Expert System and Genetic Algorithm for efficient selection and assignment of Material Handling Equipment. Expert Systems with Applications, 36, 11875-11887.
Welgama, P. S., & Gibson, P. R. (1995). Hybrid knowledge based/optimization system for automated selection of materials handling
system. Computers and Industrial Engineering, 28(2), 205-217.
Kulak*, O. (2005). A decision support system for fuzzy multi-attribute selection of material handling equipments. Expert Systems with Applications 29 310–319.
SatyaS.Chakravorty. (2008). Improvingdistributionoperations:Implementationofmaterial handling systems. Int. J.ProductionEconomics.
Sule, D. R. (1994 ). Manufacturing facilities: Location, planning and design Boston: PWS Publishing Company, 2nd ed.
Welgama, P. S., & Gibson, P. R. (1995). Hybrid knowledge based/optimization system for automated selection of materials handling system. Computers and Industrial Engineering, 28(2), 205-217.